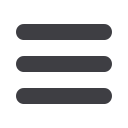

EuroWire – July 2010
31
technology news
The system revolutionises the wire drawing
process, benefiting from unique PDH
multi-function technology, enabling an
automatic control of lubrication crucial
parameters (pressure/temperature/viscosity),
including lubricant injection speed and
lubricant thermal stability. In operation, all
these parameters communicate together
in a sensitive and automatic multi-way
interaction, performing: (a) a high-density
strongly adherent anti-wear multi-layer
coat for high carbon wire (0.88–0.90%C),
deposited in 5–10 microseconds, and (b) a
nano-layer coat for plating wire.
The critical aspects of lubrication are
presently greatly simplified and some
virtually eliminated, such as friction and
wear. Instantaneous wire rod dry coating, operating with no speed limit, at zero
energy consumption (self-generated by the PDH unit), enables automatic control of
liquefied lubricant thermal stability, a vital parameter that prevents metal-to-metal
contact at the wire-die interface and permits the highest frictionless drawing speed
with a unique wear performance of about 0.1–0.3 micron per ton of wire drawn in the
last draft, and 200 tons per die in the first draft.
Spring wire is drawn from mechanically descaled bare rod, without pre-coating
chemicals, at 18m/s (3,600ft/min); 5.5mm 0.72%C rod drawn to 2.35mm at 16m/s
(3,200ft/min); 10.5mm 0.88%C rod drawn to 4.22mm at 9m/s (1,800ft/min).
In the LVC version, used in the first draft, the PDH system eliminates conventional
wire rod wet preparation, including phosphate and borax pre-coating chemicals. The
result is lower cost, improved wire quality and environmental benefits. The PDH unit is
compact, and easy to install and use.
Decalub – France
Fax
: +33 1 6020 2021
:
info@decalub.comWebsite
:
www.decalub.comWire rod lubrication by PDH system
▲
▲
Wire lubrication system for
frictionless drawing
Advertorial on behalf of Decalub
The new FRX04 wire forming and spring manufacturing machine by Numalliance is
faster and sleeker than its forerunner, released in 2008.
“This servo-driven 7-axis machine takes advantage of its tooling, gives endless
bending capability and almost deletes tooling costs for prototyping and machine
series,” explains Jean-François Counilh, CTO of Numalliance.
“The complexity of the movements allowed by
the human machine interface Touch & Form
generates a virtual 8
th
axis for the cut.”
The FRX04 covers a wide range from 0.03
"
to
0.16
"
(0.8mm to 4mm). With the option of a
laser probe and external cutter, the machine
is capable of producing parts with loops on
both ends. “The new FRX04 received a warm
welcome during the wire and tube show
in Düsseldorf,” adds Joël Etienne, CEO of
Numalliance. “We are excited about its future
applications on the market.”
Numalliance – France
Fax
: +33 329 584647
:
numalliance@numalliance.comWebsite
:
www.numalliance.comTouch & Form
Touch & Form from Numalliance
▲
▲