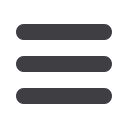

J
anuary
2012
55
›
T
echnology
U
pdate
LOOKING back 20 years ago when the
Gräbener company was running its own pipe
mill the product range encompassed steel
piles of a maximum possible production
length. This was the reason why Gräbener
Großrohr began developing milling
machines for high-quality and economical
circumferential and longitudinal weld seam
preparation on the outer surface of shells
prior to being submerged-arc welded.
Nowadays, pressure vessel and pipe
manufacturers find it hard to imagine life
without the special milling machine types for
circumferential and longitudinal weld seam
preparation manufactured by Gräbener
Maschinentechnik GmbH & Co.
KG (GMT), a member of the Graebener
Group. The 150 machines developed and
produced over the years have become
state-of-the-art when it comes to provide
vessel shells or pipes, prior to welding, with
precise seams at a reasonable cost level.
Now Gräbener took the next step on the
ladder by developing a special longitudinal
seam milling machine for the production of
wind tower segments. The machine can
be erected on the bare shop floor and is
particuarly useful because it does not need
a foundation pit.
The new floor-mounted longitudinal
seam milling machine is designed to
be used by manufacturers of offshore
wind tower segments (monopiles). The
production sites of such companies
are usually situated on the waterfront,
thus profiting from an advantageous
infrastructure, the only disadvantage
being the sandy underground of such
sites.
Considering this, the demand for a
floor-mounted milling machine, which
does without an expensive foundation pit,
was obvious.
As a consequence, the milling unit of the
machine had to be tilted by 45 degrees.
This milling position allows an erection of
the machine on the bare shop floor. Not
to forget that there are still applications
requiring the traditional version of the
machine being erected in a foundation
pit and having a milling unit working in
6-o’clock position.
In the case of the floor-mounted
longitudinal seam milling machine, the
workpieces such as pipes with external
diameters of up to 8,000mm and lengths
of up to 4,000mm are placed, aligned, and
clamped on a pipe support with adjustable
pipe rotators.
For better monitoring, a camera travelling
along with the milling process – which can
reach a depth of 90mm – is installed which
displays the process on a screen installed
in the operator’s area. For achieving a
constant milling depth during the milling
operation, the machine is equipped with
a milling height adjustment device for
automatic height copying.
Gräbener
– Germany
Email:
m.butz@graebener-group.comWebsite:
www.graebener-group.comFloor-mounted seam milling machine