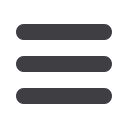

J
anuary
2012
57
›
T
echnology
U
pdate
AXTON Incorporated, located on Annacis
Island in the South Arm of the Fraser River
Delta, near Vancouver, British Columbia,
Canada, has been manufacturing heat
exchangers and other industrial equipment
since the 1980s. Its list of projects includes
the structural engineering and fabrication
of the Vancouver 2010 Cauldron for the
Vancouver 2010 Olympic Games. In 2003
Axton purchased a Model 227 orbital welding
Power Supply and Model 6 orbital tube-to-
tubesheet weld head from Arc Machines Inc,
California, USA. Although orbital welding is
generally considered to be welding of tube or
pipe, orbital welding is defined as “machine
or automatic welding in which the arc rotates
around a stationary weld joint” and this
includes orbital tube-to-tubesheet welding.
While Axton had some previous experience
with orbital welding, they gladly accepted the
opportunity to refresh their skills by having
an AMI factory trainer come to their facility to
train their lead welders.
Axton is an international company that
exports a significant amount of its production
to countries outside of Canada including
Mexico, Africa and others worldwide.
Industries served include mining, oil and gas,
chemical, acid manufacture, petrochemical,
power, transportation and pulp and paper. It
is currently fabricating a large stainless steel
exchanger for export. The tubesheet on this
unit has 990 tubes 1
3
/
4
" (44.45mm) diameter
with a wall thickness of 0.084" (2.1mm). The
vessel is 50 feet (15.24m) long and 140"
(3.55m) in diameter with tubesheets on both
ends.
The Model 227 weld power supply is
microprocessor controlled and stores weld
programs, or schedules, consisting of all the
programmable weld parameters in the power
supply memory. The weld schedule specifies
primary and background amperage, travel
speed (rotation), pulse times, wire feed
speed and other parameters. Thus, if other
factors such as tube end preparation,
cleanliness and purge flow are constant,
there is a very high degree of repeatability
from weld to weld.
The weld head features a chill follower
linked mechanically to the torch that is spring
loaded to the ID of the tube. This causes the
torch to maintain a constant distance from the
tube OD even when there is some degree
of ovality in the tubes. The chill follower as
well as the entire torch block is water cooled,
which removes heat from the ID of the tube.
This allows the application of additional heat
to the weld resulting in better penetration
without melting through the tubes. The power
supply’s arc gap control (AVC) enables the
torch to maintain a constant distance between
the tungsten electrode and the weld joint.
The Model 6 is installed using a
separate locating fixture that mounts on
the tubesheet. Efficiency is improved by
having two fixtures so that the welding
operator can position the second fixture
while the weld head is completing the weld
while mounted on the first fixture. There
is virtually no downtime between welds.
The Model 6 is a full-function weld head
with wire feed capabilities that can weld
joints with the tubes flush to the tubesheet
surface, joints where the tubes project
above the tubesheet surface or where the
tubes are recessed. All the tubes are tack-
welded in place prior to orbital welding.
The weld sequence is initiated by the
welding operator either directly from
the power supply or from the operator
pendant. The welding operator monitors
the welding through the weld lens on the
Heads-Up-Display (HUD) on the operator
pendant. The patented HUD displays weld
parameters such as Amps, wire feed and
AVC. The operator can adjust selected
parameters from the pendant while
observing the effect of the change on the
weld puddle through the lens of the HUD.
After welding, the welds get a post roll
and dye penetrant and air pressure tests at
low pressure. Tube-to-tubesheet welds are
inspected to ASME (Section VIII). Axton
has maintained ASME certification for more
than twenty-five years and achieved ISO
9001 registration in 1997, and completely
qualified to meet ASME, ISO or customer
specifications.
Arc Machines Inc
– USA
Website:
www.arcmachines.comOrbital tube-tubesheet welding
Orbital tube-tubesheet welding (above and below)