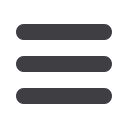

90
J
anuary
2012
www.read-tpt.com›
T
echnology
U
pdate
LANTEK has enhanced its Flex3d software
for the design, folding/unfolding and 3D
cutting of tubes, profiles and sheet metal
parts, as part of the latest 2011 version of
its software.
The new features incorporated into
Flex3d represent an advance for the
sheet metal industry, providing it with a
more flexible solution with comprehensive
functionality, capable of being tailored to
meet the needs of individual users.
Lantek Flex3d has the power to manage
large-scale projects and incorporates
advanced 3D design technologies in its
architecture. Lantek has also significantly
improved the software’s CAD data
exchange capabilities, with claimed speed
improvements of 300 per cent.
Flex3d V2011, like previous versions, is
fully integrated with all of the company’s
other applications, simplifying and easing
the management and coordination of
manufacturing processes. The new
developments introduced by Lantek are a
response to the demands of companies
within the industry, enabling them to
increase productivity and keep ahead in
the market.
Lantek Flex3d comprises eight specific
modules, enabling the user to: perform
folding and unfolding tasks; work with
tubes or profiles; carry out integrated
design and manufacture with SolidWorks
®
,
Autodesk Inventor
®
, Solid Edge
®
, CATIA
®
,
Creo Elements/Pro
®
and Siemens NX
®
;
automate the programming of laser and
waterjet five-axis sheet metal cutting
machines; and design and cut standard
profiles using the Lantek Flex3d Steelwork
module.
In the 2011 version of Lantek’s software,
all the modules incorporate new intuitive
functionality that makes 3D design and
manufacture faster and easier for the
user. Within the Flex3d product family the
company has focused on three modules in
particular.
Flex3d Tubes, developed for the design
and cutting of tubular components,
includes: new geometry macros; the ability
to automatically assign specific cutting
technology to each machining parameter;
improved simulation of five-axis cutting;
and more automated nesting capability.
These new features make it easier for
users to visualise the real results of their
tube cutting operations.
Flex3d Steelwork, intended for the
design and cutting of steelwork profiles,
is easier to use. Customisation enables
engineers to tailor the system to their
requirements and now includes automatic
screw and countersink management
to ISO standards, as well as to the
special requirements of each company.
Machining operations can be visualised
and checked faster and more efficiently in
the new version.
Flex3d 5x, aimed at programming 3D
sheet metal cutting machines with five-
axis heads, benefits from some important
improvements. Totally compatible with the
main 3D design systems used in the sheet
metal industry, the software enables users
to import parts in virtually any format ready
for five-axis cutting.
Intuitive commands lead the user through
the programming phase, greatly simplifying
the process. Other innovations include
new workbench positioning methodology,
automatic machining algorithms, and fast
and flexible verification and simulation,
all designed to improve productivity and
reliability.
Mario Rodríguez, product manager for
Flex3d, commented, “The developments
in the latest versions of our software have
produced a powerful, flexible, agile and
enormously intuitive solution that makes
3D part design and manufacture easier, in
a process that can be tailored to the needs
of individual companies.
“The new version is a major step
forward for the industry and is evidence
of Lantek’s commitment to producing
innovating systems which include the latest
technology, to help in the simplification
of design and manufacture, and to
improve competitiveness within the metal
processing sector.”
Lantek Sheet Metal Solutions
– Spain
Email:
info@lanteksms.comWebsite:
www.lanteksms.comSolution for 3D design and manipulation
of folded metalwork and tubes
SIKORA engineers have developed a new
technical feature for the company’s Laser
Series 6000 diameter gauge heads: an
integrated LED display with control panel
option.
This allows the operator to read the
diameter measuring value directly from the
gauge head.
In addition, the LED display informs
about events such as dirt in the measuring
range, and gives messages if the product
is out of the measuring range. With the
use of an externally connected control
module, the operator can set up the current
diameter nominal value up to four digits
after the decimal point. Via the line speed
or the extruder rpm the module controls
the diameter automatically to the newly set
value.
Sikora AG
– Germany
Fax: +49 421 48900 90
Email:
sales@sikora.netWebsite:
www.sikora.netGauge heads with integrated display
Laser Series 6000 now features
integrated LED display