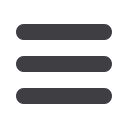

J
anuary
2012
91
›
T
echnology
U
pdate
www.larikka.comTechnologies for
tubular parts
LARIKKA
Collaring
|
Welding
|
Cutting
Welcome inside
Visit us!
Stand 6A46
LARIKKA Ltd.
Koivuhaantie 7 B
FI-01510Vantaa, Finland
Tel. + 358 20 712 1444
Innovative
Welding from inside
leaving root outside
User-friedly
Fully automatic welding process
without filling wire with clever
quick-fixing of weldable parts
Flexible
Straight or saddle weld,
Tees and manifolds
Scalable
6x1 – 219x4 mm
ilmtubepipelarikka2.indd 1
9.11.2011 15.30
OVER the past decade, Danobat has
emerged as one of the major suppliers
of individual machine tools and complete
turnkey lines to equipment manufacturers
in the OCTG (oil country tubular goods)
segment of the oil and gas industry.
Customers for Danobat’s products include
some of the most important OCTG
manufacturers.
For anyone involved in the machining of
difficult-to-machine materials such as high
specification corrosion resistant alloys,
the last thing they need is a problem with
a finish machining operation that could
result in damage to a high value component
and delays in meeting delivery dates. The
challenge that Danobat has addressed is
the design and development of machine
tools and systems capable of dealing with
increasing pipe thicknesses; tougher, more
corrosion-resistant materials; and the
demand for greater types of threads for pipe
ends and couplings, all prompted by the fact
that drilling is reaching deeper and deeper
beneath the earth’s surface.
Danobat machine tool technology
embraces the machining and threading of
pipe ends and complete machining of the
couplings that join pipe lengths together.
One of Danobat’s specific areas of
OCTG expertise is sawing technology
OCTG machining
for drill pipes, a process that involves two
Danobat CP sawing machines that move
along a slide in order to adjust the pipe
length as required. Powerful software
optimises the machining process,
integrating adaptive intelligent cutting and
blade deflection control to automatically
adjust blade speed and downfeed for
optimum performance, straightness of cut
and maximum blade life.
Once cut to length, individual pipes
can be thread to API, GOST or premium
standards by rotating the pipe in Danobat
TT and TT-B horizontal lathes. These
machines are designed on a modular basis
using finite element analysis, with the five
models in the TT range covering pipe
diameters up to 20". The main features
of these lathes, which offer the choice of
headstock on either the left or right side,
are four-axis simultaneous thread cutting
and spindle motor power up to 170kW,
depending on the model.
Danobat
– Spain
Fax: +34 943 743 138
Website:
www.danobatgroup.comHERTWICH Engineering GmbH, part
of the SMS group, has successfully
commissioned two two-chamber melting
furnaces at Otto Fuchs in Meinerzhagen,
Germany. The annual production is
50,000t, and the furnaces are equipped
with regenerative heating systems that
help to reduce energy consumption and
emissions. The new Ecomelt melting
furnaces from Hertwich Engineering are
charged from above. They operate with
integrated scrap preheating and use the
immersion melting process, which enables
them to achieve high metal yield.
SMS Meer GmbH
– Germany
Email:
info@sms-meer.comWebsite:
www.sms-meer.comNew Otto Fuchs commission
Different designs of pipe
feeding tables can be
integrated into a single-
source turnkey solution
for OCTG pipe turning
and threading