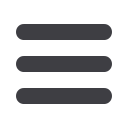

I
nspection,
M
easuring,
T
esting &
M
arking
88
M
arch
/A
pril
2007
NDT Systems & Services AG, Germany,
have designed an inspection system for
the fully automated ultrasonic inspection
of ERW and seamless tubes with
diameters from 140-400mm and wall
thicknesses from 3-25mm. For full-body
inspection, the tube is spirally guided
through several inspection basins where
probes are installed at different angles of
incidence.
Coupling is achieved by utilising the partial
immersion
technique
(PIT). In order to obtain
a high inspection speed,
a total of 60 probes
are utilised, covering
longitudinal, transverse
defects and wall thickness
measurement. Inspection
is carried out on a helical
track width of 150mm.
To ensure 100 per cent
inspection
coverage,
a 10 per cent overlap
of
the
neighbouring
scanning tracks has
been implemented for
the effective tube feed of
>135mm/revolution.
Depending on the tube diameter, inspection
velocities of a maximum of 0.35m/s are
achieved.
Angularly adjustable pairs of the helical
rolls driven by motors are used for the
helical transport of the tubes. The angle
setting depends on the tube diameter and
ranges from 7-30°.
The inspection basins, two for each
inspection mechanics, are lifted towards
the tube and lowered by a sensor-
controlled pneumatic system, ensuring
that the inspection basins are lifted only
when the leading edge of the tube has
reached a defined position. The vertical
and horizontal transverse movement
of the helically transported tube is
transmitted to the inspection basins by
means of guiding rolls.
Due to the small immersion depth and
the helical movement, coupling water
is prevented from entering the tube.
When the trailing edge has reached
the corresponding probe, the ultrasonic
electronics are automatically switched off in
order to avoid false indications.
The tubes pass the inspection line at a
distance of 1.5-2m from each other. True-
to-location in axial direction, spraying guns
mark the location of detected flaws on the
tube.
For each tube, the inspection results
are stored in the form of a strip chart
recording of the ultrasonic signal (A-scan).
In addition, they are provided as a C-scan
with coloured marking of the type and
location of the detected flaws, together with
a summarizing tube protocol.
Depending on the inspection results, the
kick-out unit sorts the inspected tubes
according to accepted or rejected.
NDT Systems & Services AG
– Germany
:
Alexander.schmid@ndt-ag.deFax
: +49 7244 7415 97
Website
:
www.ndt-ag.deScanners for wall thickness measurement
Swiss manufacturers of in-line measuring, monitoring and control systems, Zumbach
Electronic has launched a new range of ultrasonic wall thickness scanners, branded
UMAC
®
Z50 and Z100.
The transducers of the scanners can be
synchronously adjusted to the best possible
measuring position within seconds, and
can be motorised on request. The scanners
cover an outside diameter range from
5mm to 100mm (0.2" to 4") depending on
the model, and provide a simple solution
for fully non-contact, in-line wall thickness
measurement of cable jackets, tube and
hose.
The scanners are compact, allowing
installation into the cooling trough directly
after the extruder. They are manufactured
using
non-corrosive
materials
for
maintenance-free
long-life
operation
underwater. Available for four and six point
measurement, the scanners feature a
quickly removable segment to enable easy product change within a few seconds.
In combination with the Wallmaster data acquisition, processing and display system
from Zumbach, a full process control can be achieved.
Zumbach Electronic AG
– Switzerland
Fax
: +41 32 356 0430
:
sales@zumbach.chWebsite
:
www.zumbach.comUltrasonic full-body inspection system for
ERW and seamless tube
fi
Inspection basins for the detection of longitudinal defects
A total of 60
probes are utilised,
covering longitudinal,
transverse defects
and wall thickness
measurement
❱
❱
›
UMAC Z50 scanner with 6 measuring points