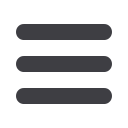

EuroWire – July 2009
46
Dies & die shop equipment
New drawing die
Lubrication is a crucial factor for the quality of the drawn wire. An interrupted lubrication in the steel wire drawing process causes an
increase of surface tension in the wire, strong pressures inside the die, rapid die wear, breakage of the drawing nib and consequent
non-programmed interruptions in the wire drawing process.
In order to avoid these problems, Koner has developed a new line of drawing dies – K. 340 and K.370 pressure drawing die (patented
worldwide), specially constructed and designed to greatly improve lubrication in dry drawing of steel wire. For wet drawing the
K.320 die has been created; its inside geometry allows optimum wet drawing process characteristics and offers economic savings.
The K.340, K.370 and K.320 methods are said to provide considerable
operating advantages:
Koner SpA – Italy Fax
: +39 02 5455832
:
tkt@tktgroup.itWebsite
:
www.tktgroup.itLaser re-cut and drilling of diamond dies
Laser drilling is still an important production process in the manufacture of diamond drawing dies. The process influences all
production steps. The diamond surface quality and the correct geometry should be as close as possible to the final finished profile.
Leyer & Kiwus Ultraschall- u. Lasertechnik GmbH is
specialised in this type of laser drilling application, with
over 20 years’ experience.
Natural diamond or PCD drawing dies processed on
the fully automatic high precision laser system, are
drilled with an accurate complete drawing profile, with
entrance, approach, reduction, bearing, back-relief and
exit. Adjusting laser settings and drilling strategies will
affect the surface quality of the drilled diamond. The result
shows a semi-finished diamond die, which needs minimal
additional ultrasonic shaping; dies are ready for the
wire-polishing and calibration process.
On this automatic machine, equipped with a 120-die
feeding magazine, drawing dies from 0.007mm up to
3mm diameter can be processed. This new laser technique
enables fast production that saves processing time, labour
and consumption costs.
Die re-cuts can be done with the Universal precision
drilling laser system. At the existing die reduction area a
micro-focused high intensity laser beam removes a thin
layer of damaged diamond. Entrance and exit angles can
be corrected. The Universal laser also drills new dies from
0.025mm up to 12mm diameter.
All laser systems are based on the newest diode pumped solid-state laser technology, with a diode lifetime greater than 10,000 hours
and power consumption less than 1.5kW.
Leyer & Kiwus GmbH – Germany Fax
: +49 241 513202
:
info@leyer-kiwus.deWebsite
:
www.leyer-kiwus.de▲
▲
Universal laser drilling system from Leyer &
Kiwus
▲
▲
A new line of dies from Koner
• Production at maximum drawing speeds
• Less machine downtime for die replacement
• Better and more homogeneous wire quality
• Wire drawing under optimum quality control
• Nib life increased by 30% compared to traditional dies
• Overall costs reduced by around 40% (only change the nib,
not the entire die)
• Application of the required quantity of lubricant coating to
the wire
• Better wet or dry redrawing operations
• Overall dimensions are the same as for traditional dies
• Savings on transport – even large quantities of nibs can be
delivered rapidly in small packages directly to customers in any
part of the world
• Elimination of die rejects and the accumulation of unusable
drawing dies. Return can be gained from the sale of worn
tungsten carbide parts