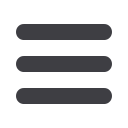

EuroWire – Luglio 2009
88
articolo tecnico
e prima dell’ingresso nel serbatoio è
pari a 10 secondi, ed il tempo effettivo
per la solidificazione del rivestimento è
approssimativamente pari a 0,42 secondi,
con un tempo di raffreddamento totale di
0,52 secondi. Secondo questa approssi-
mazione, il K2500-10 avrà un tempo
sufficiente per il rilassamento dopo l’opera-
zione di trafilatura. Per contro, nel caso
di campioni con viscosità più elevata e
campioni non casuali, questo tempo non
è sufficiente per consentire il rilassamento
e si suppone che la maggior parte delle
tensioni elastiche saranno “congelate” nel
rivestimento finale.
Conoscendo le caratteristiche reologiche
necessarie per ottenere proprietà di ritiro
contenuto ed i metodi analitici sviluppati
per valutare nuovi materiali, sono stati
condotti degli studi allo scopo di migliorare
ulteriormente le caratteristiche di ritiro
contenuto nel PVDF. Le strutture del PVDF
già identificate come caratteristiche di
ritiro contenuto sono state modificate
per perfezionare ulteriormente questo
materiale.
Due qualità commerciali esistenti di PVDF
designate come PVDF 1A e PVDF 2A sono
state identificate per determinare l’entità
del post-ritiro realizzando una serie di
esperimenti su cavi rivestiti con questi
prodotti. I rivestimenti dei cavi sono stati
applicati utilizzando una linea di estrusione
da laboratorio della società, di piccole
dimensioni, costituita da un’estrusore del
tipo Killion da 1 pollice, completo di testa
trasversale BH-30 e di tutti i necessari
equipaggiamenti a valle. Condizioni
quali la temperatura del tamburo, la
temperatura dell’acqua, la velocità della
linea e la distanza del serbatoio sono state
tutte standardizzate per eliminarle come
variabili nell’esperimento. I cavi sono
stati tagliati in lunghezze di 10 piedi ed i
rivestimenti sono stati rimossi tagliandoli
longitudinalmente. Gli esperimenti di
post-ritiro sono stati realizzati misurando
la lunghezza del rivestimento prima e
dopo un’esposizione termica di un’ora
a 212ºC. É stato concesso un tempo di
recupero di 24 ore prima di effettuare le
misurazioni finali.
Gli esperimenti di post-ritiro sono stati
ripetuti utilizzando prodotti a base di
PVDF simili, ma con alcune modifiche
della struttura allo scopo di ridurre
ulteriormente
le
caratteristiche
di
post-ritiro.
Questi campioni sono identificati come
PVDF 1B e PVDF 2B. La
Tabella 3
riporta
un riassunto dei risultati degli esperimenti
di post-ritiro.
Lequalità commerciali esistenti selezionate
presentavano caratteristiche tali da
classificarle già come prodotti a ritiro
relativamente contenuto per applicazioni
di cavi. Le modifiche apportate alle
caratteristiche reologiche offrivano gli
effetti desiderati, vale a dire la riduzione
dell’entità di post-ritiro osservato per
questo prodotto. É stato dimostrato che
tali modifiche non avevano alcun impatto
negativo sulle caratteristiche del cavo. Il
valore negativo per il PVDF 1B indica che
il cavo presentava dimensioni lievemente
superiori dopo l’esposizione termica.
Si ritiene che questa sia un’indicazione
di ritiro nullo e che il valore negativo
rientri nella gamma di precisione
dell’esperimento.
4 Conclusioni
Il ritiro post-estrusione è un problema
noto all’industria delle fibre ottiche a
causa dei suoi effetti sulle prestazioni del
cavo dovuti all’eccessiva lunghezza della
fibra. É sottinteso che il problema del ritiro
è principalmente dovuto all’orientamento
del polimero che si congela nel PVDF
dopo il processo. Il trattamento del filo e
del cavo richiede che il prodotto venga
trafilato allo stato fuso il che provoca un
allineamento significativo del polimero.
Data l’elevata velocità di rivestimento del
cavo ed il raffreddamento relativamente
rapido intrinseco al processo, molte delle
tensioni prodotte vengono congelate nel
prodotto finale. Il ritiro post-estrusione, o
post-ritiro, è semplicemente causato dal
rilassamento di queste tensioni allo stato
solido. Per limitare il post-ritiro, è possibile
ottimizzare gli utensili e le condizioni di
processo al fine di ridurre l’allineamento
del polimero ed aumentare il tempo
disponibile per il rilassamento successivo.
Le modifiche delle condizioni di processo
che consentono di mantenere il PVDF allo
stato fuso dopo la trafilatura, avranno un
effetto sull’entità totale di allineamento del
polimero restante dopo la solidificazione.
La ricerca indica che le caratteristiche
reologiche del PVDF hanno un effetto
importante sul ritiro post-estrusione. Le
strutture del PVDF che consentono un
rilassamento più rapido dell’allineamento
del polimero evidenziano un post-ritiro
più contenuto. Ridurre la viscosità è
un metodo per ridurre il post-ritiro. Un
altro metodo consiste nel modificare la
struttura del polimero per offrire una
risposta più newtoniana nell’area di taglio
inferiore. Arkema ha adottato questa
interpretazione per sviluppare nuove
qualità a ritiro contenuto per il mercato
delle fibre ottiche.
5 Ringraziamenti
Gli autori desiderano ringraziare Mara
Copolla per la realizzazione degli
esperimenti discussi nel presente articolo e
per i suoi preziosi contributi e suggerimenti
ai fini di questo studio.
n
6 Riferimenti
bibliografici
[1]
Encyclopedia of polymer science and technology,
John Wiley & Sons Inc 2007
[2]
Kynar® & Kynarflex® PVDF performance charac-
teristics and data, Arkema, 2006
[3]
Henry, James J, A study of the effects of select
processing and material variables on jacket
shrinkage in a PVDF-HFP tube-on extrusions
process, University of Massachusetts, 2003
Il presente documento è stato presentato
nel corso del 56° Seminario IWCS ed è
stato riprodotto con l’autorizzazione degli
organizzatori.
Arkema Research Center
900 First Avenue,
King of Prussia
Pennsylvania 19406
USA
Fax
: +1 610 878 6400
Website
:
www.arkema-inc.comMateriale
% di post-ritiro
PVDF 1A (qualità commerciale esistente)
2.97
PVDF 1B (PVDF1 perfezionato)
-0.28
PVDF 2A (qualità commerciale esistente)
1.22
PVDF 2B (PVDF 2 perfezionato)
0.29
▲
▲
Tabella 3
:
Esperimenti di post-ritiro su cavi in PVDF