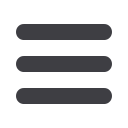

EuroWire – Julio de 2009
91
artículo técnico
Contracción limitada de
alambre y cable después de
la extrusión y la importancia
de seleccionar la calidad de
material adecuada
Por James J Henry y Nafaa Mekhilef de Arkema Inc
Resumen
Todo el mundo sabe que la contracción
que se produce después de la extrusión
puede causar problemas durante la pro-
ducción de cables de fibra óptica. En los
cables de fibras de construcción holgada
(
loose tube
) o ajustada (
tight buffered
), la
contracción posterior a la extrusión puede
causar tensiones en la fibra óptica, con
consecuencias negativas como el aumento
de la atenuación. Los fabricantes de cables
de fibra óptica tratan de resolver este
problema seleccionando detenidamente
las cali- dades de polímeros y optimizando
las condiciones de elaboración aplicadas
durante la fabricación del cable. Este
artículo analiza la selección del fluoruro
de polivinilideno (PVDF) más adecuado
y de las condiciones específicas de
procesamiento que se pueden aplicar
para minimizar la contracción después
de la extrusión, con el objetivo de reducir
sus efectos negativos sobre la atenuación
de la fibra. Se examinará la selección
de herramientas, las condiciones de
procesamiento y las características de
los polímeros que permiten limitar la
orientación del polímero y la contracción
después de la extrusión. Gran parte de lo
que se ilustra en este artículo puede ser
aplicado también a otros materiales que se
usan corrientemente para aplicaciones de
fibra óptica.
1 Introducción
El fluoruro de polivinilideno (PVDF) es una
resina específica, obtenida a través de
la polimerización por radicales libres de
1,1-diflluoroeteno o fluoruro de vinilideno
(VDF o VF
2
) que presentan una estructura
química de tipo –[CH
2
-CF
2
]n-.
Los homopolímeros PVDF son altamente
cristalinos y están caracterizados por un
módulo de flexión relativamente alto
respecto a otros fluoropolímeros. El PVDF
es a menudo copolimerizado con hexa-
fluoropropileno (HFP), clorotrifluoroeti-
leno (CTFE) y/o tetrafluoroetileno (TFE)
para modificar sus propiedades físicas
y mecánicas
[1]
.
La incorporación de comonómeros reduce
la cristalinidad, lo que reduce el módulo
de flexión y aumenta las propiedades
elastoméricas. Además de tener tipos y
contenidos de comonómeros diferentes, las
calidades de PVDF disponibles pueden ser
suministradas con distintas viscosidades
que permiten usarlas en varios procesos
de fusión. Los productos de viscosidad más
alta son adecuados para muchos procesos
de extrusión en la producción de chapas
y tubos. Los productos de viscosidad más
baja son usados normalmente para el
moldeado de inyección, tubos y la mayoría
de las aplicaciones de recubrimiento y
aislamiento de cables.
Los polímeros PVDF, como otros fluoro-
polímeros, son muy resistentes al fuego
y tienen características propias de baja
generación de humo. Las resinas no
modificadas tienen un índice límite
de oxígeno (LOI) elevado de 43 y son
clasificadas V-0 según la norma UL94
[2]
.
Hay calidades de PVDF especiales de baja
propagación de la llama y emisión de
humo que incorporan aditivos retardantes
de la llama (que aumentan el LOI hasta
100) disponibles en el mercado. Los
productos de PVDF de baja propagación
de la llama y emisión de humo son usados
normalmente para la producción de cables
plenum instalados en espacios para el
acondicionamiento del aire y en edificios
comerciales.
Los cables plenum requieren propiedades
de propagación de la llama y emisión de
humo muy bajas en caso de incendio.
Estas características se obtienen fácilmente
utilizando varias calidades de PVDF. Gracias
a estas características, el polímero PVDF
es el material preferido para el recubri-
miento de cables “
high-end
” para los cuales
se requieren propiedades excepcionales
de propagación de la llama y emisión
de humo.
El PVDF es usado normalmente para la
cubierta de cables y se aplica usando un
proceso de extrusión llamado extrusión de
tubo (
tube-on extrusion
). La extrusión de
la cubierta se realiza normalmente a altas
velocidades de entre pocos centenares de
pies por minuto hasta más de 1000 pies
por minuto. El esfuerzo de corte a través de
una hilera de extrusión de alambre puede
ser bastante alto y producir la orientación
del polímero en el material extruido.
Además, el material fundido es estirado
con relaciones de reducción (
draw down
ratio - DDR
) moderadas fuera de la hilera,
de manera que produce una considerable
orientación del polímero. Una relación de
reducción de 7:1 es típica en aplicaciones
de cubiertas de PVDF, aunque a menudo
se usen relaciones más altas o más bajas.
La acción de estirar el material extruido
fuera de la hilera genera una considerable
orientación molecular que frecuentemente
se mantiene en el material (se “congela”)
durante el enfriamiento del material
extruido. El estiramiento del polímero
fuera de la hilera seguido por temple
(
quench
) es la causa principal de la
alineación del polímero que produce la
contracción de la cubierta
[3]
. La contracción
de la cubierta, llamada corrientemente
“
shrinkback
” en inglés, ocurre cuando la
orientación del polímero “congelada” en el
material se relaja en estado sólido.