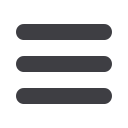

Technology News
www.read-tpt.comS
eptember
2013
83
Pipe production efficiency
MODERN, highly technological pipe
and tank construction has potential
to accelerate and optimise certain
production processes, including seam
milling technology that allows an exact
edge preparation of weld seams for the
SAW process.
Increasing yield strengths and the
application of materials of increasing
quality such as X80 require that the weld
pass of the open-seam pipe is removed
beyond the root pass. This, for example,
is a clear stipulation in the specification
for the manufacturing of offshore wind
towers, because the optimum seam
preparation is vital for an economical
and high-end welding process. The
removal of the CO
2
weld pass and the
generation of a flawless outer SAW
seam are the crucial processes for the
quality and economic efficiency of the
welding operations.
The SAW process has also been
improved by new electronic systems,
welding heads or wire/flux combinations.
Since quality and costs of a weld seam
depend on the seam type and the seam
volume, Graebener Maschinentechnik
has specialised in processes for
optimum seam geometry. When welding
top quality materials of high yield
strengths, the CO
2
weld pass must be
removed completely up to the root pass
in order to avoid welding defects.
However, some companies in
the sector of tank and apparatus
construction still remove the CO
2
weld
pass on tanks or pipe shells that have
already been tacked or welded on the
inside, by means of carbon rod gouging
with subsequent grinding, and carry out
a manual weld seam preparation.
The process of carbon rod gouging
in combination with manual grinding
and welding was considered the only
feasible process for removing the root
pass of inside welded root passes. With
this process, employees face a high
noise level, extreme heat and dust.
In addition, the accuracy of the weld
seams regarding depth guidance and
seam width suffers due to the extreme
heat brought into the material. In order
to optimise this process, Graebener
developed circ and long seam milling
machines. The weld pass is milled using
a side and face milling head while the
pipe or the tank is rotated. Welding
volume and welding time are reduced,
surface quality is increased and the
geometry of the seam volume is more
even. At the same time, the subsequent
welding process can be automated,
working conditions are improved, and
chips generated during the milling
process are recycled.
According to Graebener the costs
per metre weld seam can be reduced,
sometimes by more than 50 per cent,
by shorter processing time of the seam
preparation, reduction of welding metal,
shorter welding time and lower energy
consumption.
Graebener Maschinentechnik GmbH
& Co KG
– Germany
Website:
www.graebener-maschinentechnik.de