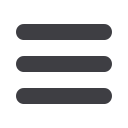

28
Mechanical Technology — July 2016
⎪
Hydraulic and pneumatic systems: power packs, compressors and valves
⎪
A
s the head of production for
SMC Pneumatics UK, Austin
has been tasked with setting
up SMC’s first pneumatics
production facility in South Africa. Austin
has been involved since the conception of
SMC Pneumatics South Africa and looks
to steer this state-of-the-art production
facility to ensure global standardisation
and that SMC’s local production capabili-
ties meet the stringent international stan-
dards of the company’s Japanese parent.
“It’s an honour to be part of the
local team and to play a key role in
Rooted in the ‘SMC way’ for 28 years, Peter Austin (left), head of production at
SMC’s new Midrand facility in South Africa, truly embodies the corporation’s culture,
philosophies and values. The new facility is now fully functional.
SMC Pneumatics South Africa looks to steer its R150-million state-of-the-art production facility towards
ensuring that locally produced components meet the stringent international standards of the company’s
Japanese parent.
State-of-the-art
pneumatic production
facility now fully operational
taking the organisation’s production
processes from start-up to success,”
Austin explains. “Creating a competitive
advantage through efficiencies, superior
quality, the right people and, ultimately,
customer satisfaction is what we strive
for,” he assures.
Thanks to its significant investment
into South Africa – exceeding R150
million – SMC aims to enrich the local
economy through job creation, skills
transfer and resources during trying eco-
nomic times. “We are starting off with a
production team of four to five people and
over time these numbers
should increase depending
on demand,” Austin says.
While skills are vital,
SMC looks to personal-
ity types as part of its
unique culture when re-
cruiting. Austin elaborates:
“Regardless of language or
nationality, what sets SMC
apart is the fact that we
always put the customer
first and this is ultimately
the common thread that
binds all 83 countries.”
SMC’s local production facilities are
situated at its head office in Midrand,
Johannesburg and became fully op-
erational from July 2016, once all the
machinery had been commissioned
and production samples signed off by
SMC Japan. “The machinery acquired
amounts to over R1.8-million and has
been sourced from the likes of Japan,
Germany, France, UK, USA and Italy.
Each piece of production equipment is
top of the range and in-line with inter-
national specifications. What’s more,
several of our CNC machines are the
first on the African continent, once again
proving that we truly are innovators in the
market,” Austin says.
The standardisation of SMC’s pro-
cesses and products around the globe
leaves no room for deviation. “SMC’s
output is all about quality and efficiency
– particularly when dealing with over
12 000 basic products and 700 000+
variations. By controlling our quality,
processes and the production of our prod-
ucts, we not only protect our reputation
as world leaders, but also ensure that
our customer’s production lines perform
at their optimum.”
Initial stages will see the production
of several line items, including various
sized cylinders, manifold assemblies, air
preparation units as well as fittings and
accessories. “Possessing such a broad
customised range means that we will
still need to make use of our extensive
international supply chain,” Austin says.
“With over 50 years experience servicing
83 countries, SMC’s vertical supply chain
ensures that we can tap into production
lines anywhere in the world for stock
whilst remaining quick, efficient and
affordable.
“SMC’s ‘customer first’ mentality has
led to us persuing localisation,” Austin
concludes. “The real benefit of local
production is quick turnaround times and
availability of non-stock items as well as
urgent parts and technical expertise in
the event of breakdowns.”
q
The testing station for pneumatic terminal blocks at the new facility.