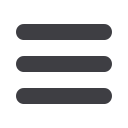

Mechanical Technology — July 2016
33
⎪
Structural engineering materials, metals and non-metals
⎪
standards and systems being used by
electrical engineering companies.
The Engineering Standards Committee
was established in London in 1901 as
the world’s first national standards
body. It subsequently extended its
standardisation work and, in 1918, be-
came the British Engineering Standards
Association, adopting the name British
Standards Institution (BSI) in 1931.
National standards were adopted uni-
versally throughout the country. These
enabled markets to act more rationally
and efficiently, with increased levels of
cooperation.
After the First World War, similar
national bodies were established in
other countries. The Deutsches Institut
für Normung (DIN) was established
in Germany in 1917, followed by its
counterparts, the American National
Standard Institute (ANSI) and the
French Commission Permanente de
Standardisation, both in 1918.
Because specification authorities
developed separately, the nature and phi-
losophy of specifications was affected by
the cultural traits of the country or coun-
tries responsible. These traits include
choices such as professionalism versus
statutory control; uniformity versus flex-
ibility; conservatism versus optimism;
and secrecy versus transparency – phi-
losophies that are also reflected in the
education systems of different countries
and in national ways of thinking.
As an example, the US standards for
welded fabrication tend towards method
specifications. Provided the methodology
is followed correctly, the risk of failure is
taken by the client. Inspection is easy. On
the other hand the European EN codes
tend towards performance standards.
Whilst more design and fabrication flex-
ibility is given, the risk is carried by the
designer/fabricator. Not surprisingly, the
EN codes appear more lenient but require
more skilled interpretation and more
competent engineering. More specific
information gathering and testing may be
required and inspection is more complex.
Initially countries were largely isolated
in terms of technology development with
specifications developing separately in
different countries. Over time organ-
isations seeking common approaches
emerged.
The League of Nations, first proposed
by US president Woodrow Wilson as part
the plan for an equitable peace in Europe,
was created in 1920 to provide a forum
for resolving international disputes. The
United States never became a member,
but the United Nations Organisation (UN)
was founded after the Second World War
with similar but broader objectives.
As international trade increased
the need for common specifications
developed. The International Standards
Organisation (ISO) was founded in
February 1947 to promote
‘worldwide
proprietary, industrial and commercial
standards’
. The USA has never been a
member.
The GATT agreement of 1948 dealt
with regulation of trade between partici-
pating countries by providing a frame-
work for negotiating trade agreements
and a dispute resolution. The World Trade
Organisation (WTO) was formed in 1995
to take over GATT responsibilities.
The European Union grew from the
1951 Coal and Steel treaty between six
countries to manage heavy industries.
These countries agreed on a common
market in 1957. Membership was ex-
panded in 1973 and the single European
act of 1987 expanded common market
flexibility paving the way for the com-
mon EN specifications and standards
we see today.
Working in conjunction to simplify
understanding, the ISO and EN specifica-
tions have moved closer together. There is
a gentleman’s agreement that attempts to
make all EN standards into ISO standards
and vice versa, but this does not work for
all standards.
Harmonised EN Standards apply only
to those that are considered relevant to
satisfying European Safety Requirements
(ESR) in products (such as pressure
vessels) in support (such as welding)
and engineering material directives.
Harmonised standards contain an appen-
dix Z, which defines which directives and
ESRs the standard meets. For example,
EN ISO 15614 for the specification and
qualification of welding procedures will
be harmonised, but other routes for weld
procedure approval may not be, such as
EN ISO 15610, EN ISO 15611, EN ISO
15612, etc.
From time to time, various countries’
standards clashed. Why? First, the base
philosophy differs, between method-
based requirements (input – what to do);
and end-specifications or performance-
based philosophies (output – what the
project or element should do). The choice
reflects local culture and the practical
consequences lie in risk apportionment.
Specifications, standards and
codes
In principle a standard is a document,
prepared and published in accordance
with established procedures that applies
collectively to codes, specifications,
recommended practices, classifications,
test methods, and guides. Standardisa-
tion refers to the process of establishing,
by common agreement, the criteria,
terms, principles, practices, materials,
items, processes, equipment, parts, sub-
assemblies, and assemblies appropriate
to achieve the greatest practicable uni-
formity of products and practices.
Standards ensure a minimum feasible
variety of such items and practices.
Specifically:
• A
specification
document is generally
considered to be a working or busi-
ness document, developed by one
entity, which may use content from
one or more standards and may alter
the said content to meet whatever
needs. They are intended to clearly
and accurately describe the technical
requirements of any given product or
process.
• A
standard
is a set of technical defini-
tions and guidelines covering specific
narrow topics that function as input for
designers, manufacturers, operators,
or users of equipment – an agreed way
of doing something. Whilst standards
rarely cover all known exceptions for
all circumstances, they are typically at
the heart of quality management and
control systems such as ISO 9000.
• Codes
are a mandatory collection of
standards, adopted by one or more
governmental bodies, or incorporated
into a business contract. Codes are
enforceable by law.
Standards are powerful tools that can
help drive innovation and increase pro-
ductivity. They can make organisations
more successful and people’s everyday
lives easier, safer and healthier. They
represent the distilled wisdom of people
with expertise in their subject matter
and who know the needs of the sectors
they represent.
The purpose of a standard is to pro-
vide a reliable basis for people to share
the same expectations about a product
or service.
Standards help to facilitate trade;
provide a framework for achieving cost
effectiveness, efficiency and interoper-
ability; and they enhance consumer
protection and confidence.
q