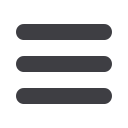

38
Mechanical Technology — July 2016
⎪
Products and services
⎪
Atlas Copco has launched the 8 Series,
a range of 10 new engine-driven air
compressors. Despite incorporating a
full-size fuel tank, aftercooler and gen-
erator, all models in the range fall below
the 750 kg weight limit and therefore
require no special driving license to
tow. Reliability, efficiency and higher
utilisation levels, coupled with superior
performance, enable the range to offer
a maximum return on investment for
Voith has unveiled its new BHS Aero-
MaXX technology turbo parallel-shaft
gear units for high-speed, high power ap-
plications at Power-Gen Europe 2016 in
Milan. The inner housing and optimised
sleeve bearings reduce power loss and oil
consumption by 30% or more.
The solution has a passive-mechan-
ical character and does not require any
additional accessories. Operators profit
Planar surface gantry for desktop applications
The compact gantry EXCM from Festo offers
maximum coverage of its working space
and is ideal for applications where every
millimetre counts. Designed using a parallel
kinematic drive concept, the recirculating
toothed belt driven by fixed motors, moves
the slide within a two-dimensional area.
Available in two ranges, the EXCM com-
bines high functionality and compact design
with an attractive price/performance ratio.
The EXCM-10 series, with an x-
axis stroke range from
150 to 700 mm,
and a y-axis stroke of
110 mm, allows for
maximum working loads
of 0.5 kg – making it ideal
for light applications such as
laboratory process automation.
The integrated motor/controller
package and plain bearing guide make this
an attractive and economical option.
The EXCM-30 series, with a precise and
robust recirculating ball bearing guide, is
designed for heavier working capacities of
up to 3.0 kg. Offering x-axis stroke variants
from 100 to 700 mm and y-axis stroke
options from 110 to 360 mm, this model
suits a wide variety of applications including
workpiece positioning, component feed-
ing, screwing and mounting.
With an optional drive
and controller package
and a z-axis inter-
face for maximum
motion flexibility,
EXCM-30 provides
an optimum solution
for small part assembly
environments.
www.festo.co.zafrom identical design standards, un-
changed overall operating behaviour and
maximum reliability. Voith emphasises
this with a 36-month warranty period –
in both new systems and retrofits. The
technology is manufacturer-independent
and available immediately.
Due to the high pitch line velocities
of up to 200 m/s, oil swirling and oil
squeezing in the gear mesh account for
a substantial part of the power loss of
high-speed turbo gear units. The BHS
AeroMaXX technology reduces these
losses by separating lubrication and
cooling.
An inner housing in the direct vicinity
of the gear set absorbs heat and dis-
sipates it into the bottom area on the
external surface on the inner housing via
cooling oil. This means that a substan-
tially smaller volume of oil is required for
the actual lubrication of the teeth contact
surfaces, while the swirling oil/air mixture
itself is minimised.
The Voith
BHS AeroMaXX
reduces losses due to oil
swirling and oil squeezing in the gear mesh.
AeroMaXX parallel-shaft gear units for turbo applications
In addition to the inner housing,
the technology also includes new BHS
EcoMax sleeve bearings on the pinion
shaft. These hydrodynamic bearings are
optimised specifically for the application,
and guarantee high-energy efficiency
along with significant oil savings.
By combining the inner housing
and the specifically designed bearings,
BHS AeroMaXX increases the gear unit
efficiency by up to 0.5%. At the same
time, oil consumption is reduced by at
least 30%. Since only passive mechani-
cal elements are used, the improvements
can be achieved without any additional
accessories or components such as
pumps or seals.
The overall operating behaviour,
design standards and dimensions of the
gear unit are also not affected by this
technology and related costs for a system
operator are amortised by the energy
savings alone within one to two years.
www.voith.comrental and construction partners.
The new compressors benefit from
Atlas Copco’s pioneering air element
design, making the compressor up to
150 kg lighter than comparable models.
During the development phase, par-
ticular consideration was given to
efficiency and the latest advances
in the 8 Series mean that fuel
consumption is reduced by an average of
12% compared to predecessors.
The largest compressor in the range
can produce 5.0 m
3
/min of air and can
still be towed by a normal passenger car
– and the inclusion of a new and updated
HardHat
®
canopy ensures the units are
tough enough for the harshest conditions.
Incorporating reliable Kubota engines,
the compressors feature an anti airlock
system for guaranteed starting. Service
is made simple as all parts are easily
accessible and simple spin-on filters are
used. The 8 Series only requires one
hour’s total service time for every two
years of operation.
The range initially comprises 10
models, ranging from the XAS 38 Kd,
with a free air delivery of 2.0 m
3
/min,
to the XAS 88 Kd, with an air delivery
of 5.0 m
3
/min. Two models in the range
also include built-in generators.
www.atlascopco.co.zaNew 8 Series compressor range launched
The XAS 88 Kd is the largest
machine in Atlas Copco’s
new 8 Series
compressor
range.