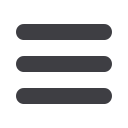

4
Mechanical Technology — July 2016
⎪
On the cover
⎪
A
tlas Copco is continuing to
expand its premium GA, GA+,
GA VSD and GA VSD+ com-
pressor ranges, most recently
with the inclusion of 200 and 250 kW
VSD (variable speed drive) versions of its
GA oil-injected, screw compressors. “We
had a gap in our VSD range between 160
and 315 kW. We have now closed this
gap with the inclusion of VSD versions for
our GA 200 and GA 250 models,” Van
Wyk reveals, adding: “while VSD com-
pressors are not widely used in mines,
we have seen immediate success with
these energy conscious clients.”
Operating at medium to high pressure
– 5.5 bar up to 13 bar – the GA range
is ideal for the manufacturing sector,
typically energising robots, actuators and
clamps on automatic production lines.
Talking about the role of VSD versions,
Van Wyk explains that if a compressor
can be run at maximum capacity, 24/7,
then the addition of a VSD is not neces-
sary. “But if the compressors are regularly
run at below maximum capacity, then it
is usually more efficient to use a VSD
to match the compressor’s speed to the
compressed air demand,” he explains.
Hence the need for the two new addi-
tions, so that compressors with smaller
motors can be used for 200 and 250 kW
VSD applications. “These additions give
us energy efficient VSD compressor op-
tions spanning the power range all the
way from 7.0 to 315 kW,” Van Wyk tells
MechTech
.
“By combining a fixed speed compres-
sor with a second VSD compressor, one
can cater for both variable demand and,
at the same time, provide a level of re-
dundancy for situations when one of the
compressors needs to be serviced. And
if full redundancy and variable flow are
required, we recommend two fixed-speed
compressors plus a VSD, with the two
fixed speeds being alternated to supply
minimum continuous demand and the
VSD providing the variable top-up flow,”
he adds.
On the ultra-high efficiency side,
Ackerman says that the permanent
magnet VSD+ range of compressors
is also being extended. “Our GA VSD+
compressors have been completely re-
designed to make best possible use
of Atlas Copco-patented permanent
magnet (PM) motor and drive train
technology.
“When used on a variable speed
application, VSD+ compressors
offer up to 50% better energy ef-
ficiency as compared to their fixed
speed siblings,” he assures.
In addition, permanent magnet
motors and the new compressor
design enable full speed operation at
better efficiencies than fixed speed
equivalents. “The PMmotor enables
a VSD+ compressor to be used at
up to 100% of its rating without effi-
ciency drop off,” Ackerman explains,
adding that the GA VSD+ range
with permanent magnet motors has
been extended to include options of
up to a 75 kW nearly twice the capacity
of the previous largest (37 kW).
Atlas Copco Compressor Technique in South Africa is expanding its offering
of industrial compressors, nitrogen and oxygen generators, air treatment
equipment, blowers and low-pressure compressors to better meet application-
specific needs in the local market.
MechTech
talks to business line managers
Charl Ackerman and Pieter van Wyk.
With the inclusion of VSD versions for its GA
200 and GA 250 models, Atlas Copco has
now closed a gap in its oil-injected screw
compressor range.
Atlas Copco’s GA VSD+ compressors have been com-
pletely redesigned to make best possible use of patented
permanent magnet (PM) motor and drive train technology.
Compressor Technique expands
“This is a game-changing innovation
for general industry. The GA 7-75 VSD+
variable speed drive compressor range
offers improved performance, silent op-
eration (down to 62 dB) and a compact
footprint, thanks to its vertical drive train
design.
“The patent-pending PM motor has
been in-house designed and is directly
coupled to Atlas Copco’s best-in-class
screw element. This technology will set
new standards in the industry for years
to come,” Ackerman believes.
Low-pressure solutions
Also expanding is Atlas Copco’s low-pres-
sure range. “Low pressure compressors
are widely used for wastewater treat-
ment; pneumatic conveying of powders
such as cement or dry food powders;
for iron smelting furnaces; and in the
chemical industry for processes such
as sulfation. Across our ranges, which
include roots and screw type blowers;
screw and centrifugal compressor op-
tions; along with multistage centrifugal
compressors, we have low-pressure solu-
tions from 200 mbar to 4.0 bar delivering
air flows from 20 to 55 000 m
3
/h,” Van
Wyk notes.
“In the past, we have been weak in
this area. We had a screw (ZS) and a
centrifugal (ZB) offering, but these had
a maximum capacity of 160 kW. Our ZS
offering now goes up to 355 kW, and
these also now include VSD options,”