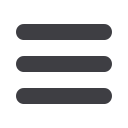

Mechanical Technology — July 2016
5
⎪
On the cover
⎪
range
to better meet client needs
he reveals. “The centrifugal ZB range
was previously limited to 132 kW, but
we can now go up to 250 kW, with VSD
options available for most compressors
in the range,” he says, adding, “we can
also cater for larger flows and sizes with
our multistage centrifugal (ZM) range.
“In the municipal space, we have had
visibility problems. Wastewater plant op-
erators seldom know about the difference
between screw and centrifugal technolo-
gies. All they know about is the common
roots-type blower, which is not always
the most effective or efficient option.
“Going forward, we can now offer
best-fit solutions for almost any applica-
tion requiring low pressure compressed
air,” he explains, before suggesting that
“the different technology options and
their advantages really need to be prop-
erly introduced to the market”.
Nitrogen and oxygen generators
Another key product for Atlas Copco
Compressor Technique is its range of
nitrogen and oxygen generators. “Com-
pared to the on-demand ordering of gas
bottles or tanks, on-site production of
nitrogen or oxygen offers cost savings,
flexibility and continuous delivery advan-
tages,” says Ackerman.
For nitrogen production, two technolo-
gies are available: membrane separation
and pressure swing adsorption. “Purities
of up to 99.999% can be achieved with
either technology but the membrane
technology is less efficient for producing
high purity nitrogen, requiring an air to
nitrogen ratio of about 7:1 to produce a
99,999% purity. Pressure swing adsorp-
tion, on the other hand, can achieve
that purity with a 4:1 ratio,” Ackerman
explains.
“But for lower purities, membrane
technology becomes more efficient, with
a purity of 98% being the break-even
point between the two. So for nitrogen
purities between 95 and 98%, we recom-
mend using membrane technology, while
for higher purities, our NGP swing ad-
sorption solution is better,” he suggests.
Typical uses of lower purity nitrogen
include inflating car tyres (95% purity)
and fire suppression. “For food preserva-
tion applications, such as filling potato
crisp packets with nitrogen before sealing
them, or for preserving maturing wine,
99.5% is required. And we have recently
supplied high-purity units in Cape Town
for packaging biltong,” Ackerman says.
Van Wyk adds: “Food and beverage
industries are less affected by the down-
turn, so we are experiencing strong sales
growth for all of our products at food,
chocolate, soft drink and beer manufac-
turing plants.”
Membrane technology separates
nitrogen in compressed air from oxygen
and water vapour. The compressed air is
passed into the cores of bundled semi-
permeable membrane fibres. The larger
nitrogen molecules travel directly up the
cores to the outlet, but the smaller oxygen
and H
2
O molecules permeate under pres-
sure through the membrane walls and are
discharged to atmosphere.
“The technology can produce rela-
tively high volumes and since water
vapour also permeates, the nitrogen is
inherently dry,” Ackerman says.
PSA adsorption, on the other hand,
relies on molecular sieves, which work
in a similar way to desiccant dryers.
If producing nitrogen, the sieves trap
and isolate oxygen and water vapour
molecules, allowing the nitrogen to pass
through. The principle can also be used
to produce high purity oxygen, however.
In this case, the sieve material isolates
the nitrogen molecules and the oxygen
passes through.
Once the molecular sieve material in
a vessel is saturated, the unit ‘swings’
over to a new adsorption vessel, while
the saturated one is regenerated. “This
is done simply by releasing the pressure
and allowing the trapped gas to discharge
to atmosphere.” he explains.
For foundry use and for laser cutting
applications, for example, the compres-
sors, nitrogen or oxygen generators, tanks
and pressure boosters can be assembled
onto a common skid. “So we can deliver
a plug-and-play gas solution to foundries
and fabricators – and by using a pressure
booster, we can typically provide nitrogen
to a laser cutter at 25 bar and up to
40 bar, if needed,” he adds.
Specialised solutions
Atlas Copco also offers specialised
compressor ranges for key industries.
“We have a railway range, for example,
which will be very useful for the new
rail rejuvenation projects currently be-
ing implemented in South Africa. Our
GAR railway compressors are used for
operating brakes, doors and toilets on
train locomotives and coaches all over
the world and will be ideal for use on the
600 Alstom X’Trapolis Mega passenger
trains being built in South Africa by the
Gibela Rail consortium for PRASA or by
Bombardier for the new Transnet Freight
Rail fleet currently under construction,”
Ackerman says.
A full medical range, which conforms
to the SANS 7396 standards for medical
gases is also on offer for hospital qual-
ity air – for breathing and for powering
surgical instruments.
“These expansions are enabling us to
be competitive in a much wider range of
applications,” continues Van Wyk. “And
while Atlas Copco has deliberately cho-
sen to operate in the premium segment
of the market with a broadening product
range, increasingly, customers are un-
fairly comparing our full-featured quality
products to lower cost brands,” he says.
“So we have also launched Atlas
Copco ranges that maintain our qual-
ity standards but do not have all of the
functionality and class-leading energy
efficiency associated with our flagships.
These are simpler, less expensive ver-
sions that preserve the quality and
reliability associated with Atlas Copco
branded compressors and air treatment
products.
“Along with all of our other range ex-
pansions, these further enhance our pre-
ferred supplier status.” he concludes.
q