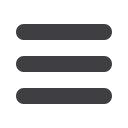

Chemical Technology • October 2015
20
PUMPS & VALVES
place after 90 days of primer application, the baseplate
will need to be recoated with primer.
• F For modularised pumps, consideration should be given
to pregrouted baseplates.
Couplings and guards
Elastomeric and disk type spacer couplings are used for
connecting pump and driver shaft ends. Progressive cavity
pumps are driven by lubricated universal joint. While disk
spacer couplings are preferred for all applications, the
manufacturer’s standard coupling design for vertical in-line
pumps can be accepted. API 671, 4
th
Edition, based special
purpose couplings should be specified when continuous
operating speed is over 3 600 rpm.
The standard requirements for disk type spacer cou-
plings are:
Monitoring instrumentation guidelines
• API 670, 4th Edition based monitoring instrumentation
should be specified for pumps fitted with hydrodynamic
bearings and rated 1 118 KW (1 500 HP) and above.
This requirement also applies to pump drivers (steam
turbines, electric induction motors and gear units, if
furnished).
Radial bearings
• X-Y pair of non-contact proximity probes for each ra-
dial bearing Two-(2) Resistance Temperature Detectors
(RTDs) per bearing
• Thrust bearing
• Two-(2) axial position non-contact proximity probes
• Two-(2) Resistance Temperature Detectors (RTDs) per
side (active and inactive); total four-(4) RTD’s per bearing
Phase reference probe
• On motor and steam turbine shaft ends.
Winding temperature RTD’s
• Two-(2) per phase; total six-(6) RTDs
Casing accelerometers
• One accelerometer each on pinion and gear sides
• Casing accelerometer should be furnished for direct act-
ing reciprocating pumps above 150 KW.
Pumps fitted with hydrodynamic bearings and with rated
power between 746 KW and 1 118 KW should have provi-
sion for installing non-contact type radial vibration and axial
displacement probes. RTDs should be furnished for pump
and driver radial and thrust bearings.
Vibration, thrust position and bearing temperature-
related shutdowns are generally dictated by plant operating
and safeguarding philosophy and should be agreed to by
all parties involved in equipment selection, including the
equipment manufacturer.
This article first appeared in ‘Pump Engineer News’ published
by KCI Publishing.
www.pumpengineer.netA.
Minimum service factor:
(Standard SF=1.5 for
Disk/Diaphragm Couplings)
1.0 for constant torque applications
1.25 for pumps driven by motor + gearbox
1.5 for P.D Rotary pumps
2.0 for Reciprocating Pumps 125 mm (5’’ standard)
B.
Minimum spacer length:
125 mm (5’’ standard)
C.
Standard shaft end:
* Cylindrical with rectangular key, or
* Taper shaft end as dictated by API 610, 10th Edition, Para 6.2.8)
* Fits and tolerances on fits to be as per AGMA 9002-A86.
* Taper shaft end with hydraulic fit should be specified for centrifugal pumps when power rating exceeds 1500 KW.
D.
Material
Corrosion resistant steel
E.
Minimum Balance Grade
AGMA 9
F.
Coupling Guard
In accordance with API 610, 10th Edition, Para 6.2.14 except that non-metallic guards as stated in 6.2.14 c) are not acceptable. Specify non-
sparking metallic guard