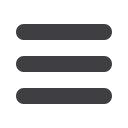

Chemical Technology • October 2015
18
Lubrication of pump bearings
Standard methods of lubrication are:
A Grease
B Wet sump with oil ring or oil flinger
C Purge (wet) or Pure (dry sump) oil mist
D Forced oil
E Bearings lubricated by pumped fluid as in the case of
magnetic drive pumps and vertical line shaft pumps.
1. The first three types of lubrication methods are used for
anti-friction bearings.
2. Forced or pressure oil lubrication is applied to hydrody-
namic bearings.
3. Oil lubrication is the preferred method over grease
lubrication.
Minimum specification requirements and
limiting conditions grease lubrication
• A Greased bearings should be used when oiled bearings
cannot be used; such as in cryogenic services where
the fluid temperature may be close to pour point of the
mineral oils or where access is limited or where leakage
of oil can be hazardous or surrounding atmosphere is
laden with soot, dust, or ash particles.
• Most calcium, barium and lithium based greases have an
operating temperature range of -30 to +120 ºC. Organic
thickener grease such as alkoxyfluoroether oil based
grease have a higher range; - 40 to + 250 ºC. Greases with
solid lubricants are normally used for mixed/boundary
friction. During operation, thickeners in grease together
with wear particles gradually form abrasive paste which
in turn, may induce further wearing of bearing elements.
• When sealed bearings are required, engineers should
specify “Sealed for bearing life” greased bearings. Use
of sealed greased bearings is usually limited to operating
temperatures not exceeding 100 ºC.
Oil lubrication
• Wet sump with oil flinger is the preferred method of
lubrication for horizontal pumps.
• Pump bearing housings should have non-contacting, laby-
rinth type seals as a standard to preclude atmospheric
contaminants from entering the housings. For pumps
installed outdoors in dirty environments (loose fly ash,
soot, dust, sand etc.), magnetic type bearing isolator
seals should be considered to achieve positive isolation
of bearing housings from the environment, especially
when the pump is not in operation.
Pump selection and
application guidelines – Part 2
A standard set of considerations and best
industry practices that Rotating Equipment
Engineers apply in the selection of various
types of pumps and their auxiliaries, is
described. Typical services and limiting
operating conditions of centrifugal and
positive displacement pumps are included
to aid in the selection process. Part 1
appeared in the August 2015 issue.
by Neetin Ghaisas, ME, PEng, Director of Design Engineering and Rotating Equipment
Group Leader at Fluor Canada, Calgary, Alberta, Canada