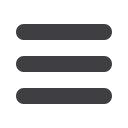

Chemical Technology • October 2015
14
Adapting valve designs
to meet industry’s exacting
requirements
I
n sterile process engineering, such as in the production of
insulin, vitamin enzymes or APIs (Active Pharmaceutical
Ingredients highly potent agents), users place special de-
mands on the hygienic valves that they use. This is particularly
apparent in the exacting requirements regarding the produc-
tion process and the materials. There is a noticeable trend
here: “Operators are continually demanding higher quality
materials. In the pharmaceutical sector, stainless steel grades
such as 1.4435 are usually used. However, users are increas-
ingly requesting 1.4359 and Hastelloy qualities,” reported
Alfred Knöbl, product manager of the SISTO-C series at SISTO
Armaturen SA Echternach, Luxembourg. “This is because
these materials are far more corrosion-resistant. The valves
are not necessarily affected by the cleaning liquids used in
the CIP/SIP processes, but rather by fluids that are needed
for product processing, for example after fermentation.”
In old systems a lack of space was a common problem
and it is also an issue in new biotech systems. This has given
rise to the present trend of building production facilities in an
increasingly compact way, often grouping together multiple
valves as valve manifolds. As a result, many valve manifolds
are frequently installed under the tanks. Froma hygiene point
of view, this new design offers nothing but advantages, as
Knöbl explained: “The compact design reduces the neces-
sary distances between the valves and eliminates dead legs
in the piping.”
Another trend that has an impact on the production pro-
cess is the increasing use of very small nominal diameters.
Typical nominal diameters used in the pharmaceutical sector
range from DN 8 to DN 50; most are between DN 15 and
DN 20. However, valves with a nominal diameter of DN 2 are
also needed sometimes. “These are not laboratory applica-
tions,” clarified Knöbl. “Producing such nominal diameters is
a big challenge in terms of the production process.” For this
reason, in addition to establishing new production processes
at SISTO, the necessary measuring methods and quality
monitoring systems were also set up.
Very low flow rates are also needed in processingmethods
such as chromatography, for example. Another particularity:
these applications require a very high compressive strength in
some cases and operating pressures of 20bar are quite usual.
“In normal pharmaceutical production we have operating
Hygienic diaphragm valves are needed
for a wide variety of applications in the
pharmaceutical and biotech sector.
Having paved the way for reliable aseptic
production with its unique design years
ago, the SISTO-C series is continually
adapted to meet industry’s increasingly
stringent requirements.
by Bryan Orchard