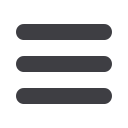

Dies
Wire & Cable ASIA – January/February 2011
59
Re-grinding in-house
Ajex & Turner has manufactured a wide range of wire drawing dies, tools and
machinery since 1962, dedicated to improving the equipment and technology
with a policy of ongoing development.
New die polishing machines are now available. For PCD and ND wire and
stranding dies up to 20mm, the model SAU 450 can re-grind and polish dies from
0.5mm. An in-built grinder automatically grinds the needles in any degree. In one
working shift, up to 20 large dies can be re-ground and polished, depending on the
PCD blank size.
Also available is the UPM-515 with swinging head. This machine, believed unique
to Ajex & Turner, has been developed for polishing and re-cutting diamond and
PCD dies up to 3mm. It has a built-in generator, to save space, and is easy to
operate. The ultrasonic frequencies of this machine are said to be very stable,
while the oscillating head removes sharp edges and produces well blended angles.
For 3mm, it takes 20-40 minutes in shaping, depending on the PCD nib size.
For in-house grinding of carbide dies the company offers model TCD-11, suitable
for grinding and polishing carbide dies of 1mm to 50mm. It can also hold a casing
size of up to 100mm. Depending on nib size, up to 50 dies can be ground and
polished in one working shift.
Ajex & Turner can also supply accessories such as diamond powder, pastes and
steel and diamond needles.
Ajex & Turner Wire Die Co – India
Fax
: +91 11 2745 2640
:
sales@ajexturner.comWebsite
:
www.ajexturner.comNew drawing die
Lubrication is a crucial factor for the quality of the drawn wire. An interrupted lubrication in the steel wire drawing process
causes an increase of surface tension in the wire, strong pressures inside the die, rapid die wear, breakage of the drawing nib
and consequent non-programmed interruptions in the wire drawing process.
In order to avoid these problems, Koner has developed a new
line of drawing dies – K.340 and K.370 pressure drawing die
(patented worldwide), specially constructed and designed to
greatly improve lubrication in dry drawing of steel wire.
For wet drawing the K.320 die has been created; its inside
geometry allows optimumwet drawing process characteristics
and offers economic savings.
The K.340, K.370 and K.320 methods are said to provide
considerable operating advantages:
Production at maximum drawing speeds
•
Less machine downtime for die replacement
•
Better and more homogeneous wire quality
•
Wire drawing under optimum quality control
•
Nib life increased by 30% compared to traditional dies
•
Overall costs reduced by around 40% (only change the
•
nib, not the entire die)
Application of the required quantity of lubricant coating to the wire
•
Better wet or dry redrawing operations
•
Overall dimensions are the same as for traditional dies
•
Savings on transport – even large quantities of nibs can be delivered rapidly in small packages directly to customers in
•
any part of the world
Elimination of die rejects and the accumulation of unusable drawing dies. Return can be gained from the sale of worn
•
tungsten carbide parts
Koner SpA – Italy
Fax
: +39 02 5455832
:
tkt@tktgroup.itWebsite
:
www.tktgroup.itK.340, a new line of dies from Koner
❍
❍