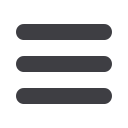

Wire & Cable ASIA – September/October 2007
65
Wire & Cable ASIA – January/February 11
Ceeco Bartell believes its roll form strander is the only
process to fully utilise the advantages of single input
wire (SIW) diameter. SIW represents a strand and design
mentality, with a manufacturing methodology that
effectively reduces the conversion cost from rod to strand
without compromising conductor performance.
This concept replaces the traditional stranding of wires
using different wire diameters with the stranding of wires
using the same wire diameter for a wide range of cross
sections. SIW diameter meets major conductor standards
such as IEC 60228, HD 383 and the ASTM standards. By
incorporating a single input wire diameter program into the
strand design, significant savings can be achieved in wire
drawing, stranding and the insulation processes.
Traditionally a finished stranded conductor requires its
own drawn wire diameter. Each wire diameter typically
requires a new string-up in the wire drawing machine.
Some conductor designs require more than one drawn wire
size. The set up time taken on the drawing, combined with
inventory levels that are necessary to manage the number
of wire diameters, represent unnecessary activities that
add to the cost of conversion from rod to strand.
The SIW approach, using the same input wire diameter to
finish a range of stranded conductors, eliminates much of
the unnecessary activity associated with the traditional set
up.
This leads to increased efficiency in the wire drawing
process. Instead of having to produce a large number of
different wire sizes only one or two are required using the
SIW system.
The improvements can be seen in the following areas:
Higher productivity in wire drawing
•
Lower drawn wire scrap
•
Quicker set-up
•
Reduced work in process
•
Shorter cycle times
•
Smaller input wire storage area
•
Reduced drawing die inventories
•
The single input wire method can
save between 15% and 20% on
wire drawing costs, including the
elimination of re-strings for size
changes, lower die inventory and
reduced in-process wire.
Double twist stranding has always
been among the most productive
methods of producing strand. Its
incorporation into the roll form
strander, with the application of the
individual shaping of the wire, has
further extended its performance
range.
In
Figure 4
its performance can
clearly be seen. Each machine type
works the wire differently, and this
impacts on the strand design that
can be used for that process.
Figure 4
highlights some of the
advantages and disadvantages of
each machine type as they relate
to product capability and relative
cost. It is important to recognise that if the roll formed or
die shaped wire is used in the strand construction a ‘rigid’
machine, or a machine that puts a twist in the wire for each
lay length, is a prerequisite for manufacture.
Capital cost per twist
Determining the range of equipment to cover the strand
designs is an important consideration in achieving the
lowest conversion cost.
For example, the double twist machine offers the lowest
cost per twist but is the most limiting in terms of the
construction possibilities. By its incorporation into the roll
form strander this range of construction possibilities has
been greatly expanded. The planetary machine, at the
other end of the spectrum, has the highest cost per twist
but the greatest construction possibilities, which is why it
is used for special purpose products.
Material limitations
Each machine type works the wire differently. For this
reason alone it is necessary to identify the differences to
be able to use the same drawn wire size for the multitude
of stranding possibilities.
This applies not only to the principle of the machine
but also to the area reduction that can be expected
from different machine types. Keep in mind that in most
cases the area reduction through the machine varies at
different speeds and, to some extent, all machines used
to manufacture strand require that the stress in the wire
during the stranding point exceed the yield point of that
material.
For example, the double twist, single twist and rigid
strander put a twist into each input wire along the axis
of the wire for each lay length; the tubular and planetary
machines are more forgiving and put almost no twist into
each wire, which is important when stranding steel wire.
Lay and layer limitations
Both the double twist and single twist machines currently
can manufacture up to four layers (typically a 37-wire
Figure 5
❍
❍
: Line speed comparisons
Conductor size (mm
2
)
Line speed comparison aluminium
Single twist
Line speed (metre per minute)
RC double twist
Ceeco Bartell