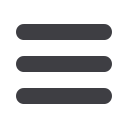

EuroWire – November 2010
69
technical article
It further allows more precise distribution
of wire tension in each layer, optimising
the straightness of the resulting conductor.
The shaped conductors are formed into a
compact unilay strand using a high-speed
double twist strander. The machine is a
side-loading unit equipped with a standard
floor loader, designed to load and unload
the take-up reel with minimum operator
effort. The scope of products that can be
manufactured includes:
Copper and aluminium stranded
•
conductors between 8AWG and
600kcmil or 10mm
2
and 300mm
2
Bunched conductors to compact
•
strand with fill factors between 76%
and 97%
Aluminium conductors steel reinforced
•
(ACSR) using a single steel wire core
All aluminium and aluminium alloy
•
conductors (AAC & AAAC)
Cabling of insulated conductors
•
Ceeco Bartell believes its roll form strander
is the only process to fully utilise the
advantages of single input wire (SIW)
diameter. SIW represents a strand and
design mentality, with a manufacturing
methodology that effectively reduces the
conversion cost from rod to strand without
compromising conductor performance.
This concept replaces the traditional
stranding of wires using different wire
diameters with the stranding of wires using
the same wire diameter for a wide range
of cross sections. SIW diameter meets
major conductor standards such as IEC
60228, HD 383 and the ASTM standards. By
incorporating a single input wire diameter
program into the strand design, significant
savings can be achieved in wire drawing,
stranding and the insulation processes.
Traditionally a finished stranded conductor
requires its own drawn wire diameter. Each
wire diameter typically requires a new
string-up in the wire drawing machine.
Some conductor designs require more
than one drawn wire size.
The set up time taken on the drawing,
combined with inventory levels that are
necessary to manage the number of wire
diameters, represent unnecessary activities
that add to the cost of conversion from rod
to strand.
The SIW approach, using the same input
wire diameter to finish a range of stranded
conductors, eliminates much of the
unnecessary activity associated with the
traditional set up.
Capital cost/
Twist
$
Double twist
Strander
$
Tubular
Strander
$
Drum
Twister
$
Rigid
Strander
$
Planetary
Strander
Double Twist
Strander
Tubular Strander
Drum Twister
Rigid
Strander
Planetary
Strander
Factors
Capital cost/twist
1
3-5
7-16
9-12
16-24
“Working
factor”
Significant
(rigid)
Almost none
(planetary)
Significant
(rigid)
Significant
(rigid)
Almost none
(planetary)
Lay limitations
Unilay only
Not applicable
None
None
None
Layer limitations
Up to 4 layers
2 layers
None
None
None
Typical payoff
package
Stem
Bobbin
Stem
Bobbin
Bobbin
Payoff mode
Continuous
Required
loading cycle
Continuous
Required
loading cycle
Required
loading cycle
Single input wire schedules
Compact
Six wire sizes required using a conventional system
One wire size required using SIW system
Figure 1
▲
▲
:
Close up of roll formers
Figure 2
▲
▲
:
Roll form unit and closing point
Figure 3
▲
▲
Figure 4
▼
▼
:
Process cost/twist comparison