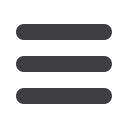

41
CONSTRUCTION WORLD OCTOBER 2016This flexible needle punched nonwoven paving fabric has been
used in a recent road surfacing project in Zambia. To gain access
to one of the world’s largest copper mines at Kalumbila on Zambia’s
Copper Belt, a network of dirt roads off the main road between Solwezi and
Lumwana needed to be constructed. The new mine is remotely located.
“All road building materials had to be transported over long distances
and at great cost,” says Chris Powell, Fibertex South Africa – manufacturers
of geosynthetic products. “High seasonal rainfall in this region has a detri-
mental effect on roads, substantially increasing maintenance requirements.
“To lower the costly routine maintenance intervals on these roads,
they were later upgraded to a surfaced standard, using Fibertex AM-2
paving fabric. Fibertex AM-2 has added thermal bonding on one side
only. The purpose of this pre-compressed 140 g/m² polypropylene (PP)
bitumen-saturated paving fabric is to prevent the ingress of surface water
into the selected layers of the road prism, thereby reducing the bearing
capacity of these layers.
“This membrane also act as a Stress Absorbing Membrane Interlayer
(SAMI) to prevent surface stress cracking by absorbing stresses imposed
by differential loads. This paving fabric also prevents the propagation of
stress cracks from lower surface layers (older asphalt or chip seal layers)
in the case of a road reseal.”
By including Fibertex AM-2 in the reseal design, the formation of stress
cracks and eventual pothole formation is prevented, thus extending the
service life of the road surface.
Additionally, when using Fibertex F-grade geotextiles in a separation
application below the layer works of the road prism, the road design can be
altered to include less of the costly imported engineered fill. This reduces
the thickness of the selected layers, resulting in a more cost effective design.
Without the use of a separation fabric in weak subgrade conditions,
intermixing of engineered aggregate into the weak subgrade could occur.
As a result, the bearing capacity of the base course is reduced, which could
lead to base course failure of the road.
The Fibertex AM-2 system can be appliedmechanically for large volume
installations, as well as manually in cases where narrowwidth installations
are required. An extensive range of nonwoven geotextiles is manufactured
at the Fibertex manufacturing facility in Hammarsdale, KwaZulu-Natal, in
accordance with major international quality standards. These include ISO
9001: 2008 accreditation, the coveted CE-marking and other quality, safety
and environmental specifications. Extensive quality testing to ensures
nonwoven products meet customers’ requirements.
ZAMBIAN ROAD PROJECT
FAR LEFT:
Fibertex AM-2 paving
fabric prevents the propagation of
stress cracks from lower layers,
when placed between old and new
asphalt layers.
LEFT:
Fibertex AM-2 paving
fabric is designed especially for
civil engineering, mining and road
construction and maintenance
projects, includes a paving fabric
– Fibertex AM-2.This flexible
needle punched nonwoven paving
fabric has been used in a recent
road surfacing project in Zambia.
The Fibertex range of geotextiles, which is
designed especially for civil engineering, mining
and road construction and maintenance projects,
includes a paving fabric – Fibertex AM-2.
>