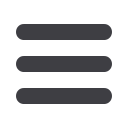

CAPITAL EQUIPMENT NEWS
SEPTEMBER 2015
30
C
ertain aspects of running business-
es, such as operational efficiency,
are universal. And efficiency in one
area of expertise that has an exponential
effect on the rest of the business is an
elusive pot of gold for most. The open-
cast mining sector – if approached with
a solution that guarantees it massive sav-
ings in time, money and material volumes
– would be swift to implement it.
This has been the case with stemming
trucks supplied to the southern African
market through a partnership between
Scania South Africa and Cobra Petro
Projects. An initial truck was manufac-
tured and introduced to the market at last
year’s Electra Mining Africa exhibition. One
of South Africa’s most established mining
groups saw it and arranged a demonstra-
tion review. The truck impressed the com-
pany to the extent that it purchaced the
demo model. Within a few months two oth-
er units were purchased. Cobra Petro Proj-
ects manufactures the units under license
of Ausroads making use of Scania trucks.
“The process of stemming in a local
opencast mining context is traditional-
ly archaic as the most common practice
involves crudely modified front-end load-
ers to backfill blast holes,” explains Chris
Swanepoel from Scania South Africa’s
mining division.
He points out that this method is ineffec-
tive, labour intensive and results in incon-
sistent blasting results. In addition, backfill
material either consists of aggregate that
needs to be transported to the blast site or
of the rock displaced through the drilling of
the blast hole.
This means that the material is not graded
and specific to the requirements of the blast
– which affects efficiency.
“Use of this new stemming truck technology
eliminates all these variables and ensures
the correct amount of precisely sized ag-
gregate into blast holes in the most efficient
way possible,” states Karel Steyn, technical
BLASTING SOLUTION:
a game changer for opencast mining
The trucks are manufactured to
stringent standards.
Aggregate being dispensed.
A 3 400 litre water tank feeds the dust
suppression system comprising water jets
around the aggregate spouts, plus a pair of
powerful jets located at the rear.
A completed truck ready for delivery.