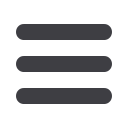

CAPITAL EQUIPMENT NEWS
SEPTEMBER 2015
31
manager at Cobra Petro Projects.
“Precise measurements of aggregate can be
inserted through the truck’s load-cell sys-
tem and this means no wasted material, no
wasted time and the provision of the exact
amount of resistance for the blast.”
Other benefits of using the stemming truck
include operational safety (one truck and
operator) versus several smaller vehicles;
being able to access hard-to-reach blast
areas with an 8 m boom conveyor (170 de-
grees) and significantly decreasing the time
between charge and blast to an almost neg-
ligible period.
Aggregate flow control and rear boom ma-
noeuvring can be carried out through a joy-
stick mounted in the cab or via a wireless
remote control from outside the vehicle. A
neatly integrated control screen fitted into
the dash allows the operator to keep a close
eye on the amount of aggregate delivered
or that remaining in the hopper, and another
notes the vehicle’s gross vehicle mass.
The trucks are available in two configura-
tions:
• 13 m
3
hopper
• 16 m
3
hopper
Elements of the unit as well as the interior
of the cab can be suited to exact client re-
quirements. As the trucks are manufactured
locally, clients benefit from local support
teams and spare part availability.
Scania and Cobra Petro Projects are proving
that the incorporation of such game-chang-
ing stemming truck technology guarantees
increased blasting efficiencies across the
opencast mining sector in southern Africa
which can in turn increase production – ulti-
MINING
mately resulting in higher profit margins in a
repressed commodity down cycle.
b
Written by Richard Jansen van Vuuren
Photographs:
Jade Photography and Eventco Strategic Marketers:
Scania and Richard Jansen van Vuuren
A stemming truck under construction at Cobra Petro Project’s facility in Johannesburg.
One of the three conveyor belts present
on all trucks.
All trucks are fitted with an eight metre boom conveyor (170 degrees). Karel Steyn, technical manager at Cobra Petro Projects.
What is stemming?
Stemming is a key element in the ‘drill and
blast’ mining technique. In stemming, material,
such as fine gravel that is called aggregate, is
placed on top of explosives in drill holes. When
the explosives are detonated, the stemming locks
the expanding gases and keeps the forces in the
borehole until rock begins to break. A stemming
truck’s duties are to fill blast holes on a mine site
into which the explosive charges have already
been inserted. Typically these are located at five-
metre intervals in the area to be broken up. A
16 m
3
load can fill up to 60 holes, and stemming
truck can easily deliver 500 kg in 15 seconds,
allowing excellent productivity on site.
Source: Scania