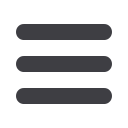

154
M
ay
/J
une
2007
New trends for tube and profile separation
concepts by shear and cold rotary saw
By Ing Jan Attl, Attl a spol sro, Prague, Czech Republic
Background
Attl a spol sro was established in 1921 by two brothers, Karel and
Alois Attl. The factory successfully designed and produced small
forming machines for both the domestic market, the European
export market, South America and Palestine. The company was
nationalized in 1951 and returned again into the ownership of the
Attl brothers, this time Jan and Karel, after the Velvet Revolution in
Czechoslovakia in 1989.
Since 1992 the company has been designing and manufacturing
production mills for open profiles and has grown to specialise in
mills for longitudinally welded tubes and profiles. Attl a spol sro can
supply a tube mill from a single source, which is a special capability
in Europe. The company has developed its own knowledge-base
for the decisive components of a mill. These are:
• Vertical strip accumulator
• Calibration of profiles and tubes
• Forming and calibrating sections of the mill
• HF welding generator
• Flying shears cutoff in combination with flying cold rotary saw
• Bundling machine for profiles and tubes at the exit of the mill
Attl a spol sro invests considerable effort in the development and
design of these above individual components, as their standard
decides the productivity, life and overall parameters of a mill.
In the mills produced by Attl, it is possible to cater for practically all
types of longitudinal welding of profiles and tubes, such as:
• HF generator – own design
• TIG; Plasma
• Laser – Trumpf; Rofin
In the following article, the details will be presented for one of the
most important components of the mill – the flying cutoff machine
for profiles and tubes.
Introduction
Since 1996, Attl a spol sro has, in addition to the process of dividing
by flying saw, facilitated 14 different applications of dividing tubes
and profiles by shear. It is the findings, suggestions and conclusions
based on this experience that will be detailed here. It is the aim of
this article to be clear and conclusive.
Next to a HF welding generator, the efficiency of the flying cutoff
machine has a decisive influence on the capacity of the whole
production mill. However, here we will not evaluate the ability to
divide tubes or profiles in regards to the production speed and
tolerances of the cut length. These aspects have been sufficiently
mastered and will not be addressed here.
This article will focus on the issues involved in comparing the
individual types of dividing the tubes and profiles, by rotary saw
versus shearing. Issues include quality of the shear plane, dividing
time, financial concerns regarding production times, energy savings
and last but not least, ecology.
Evaluation of cutting profiles
with cold rotary saw
Cutting by cold rotary saw is currently the most commonly used
method to divide profiles and tubes, since it leaves a high quality
cutoff face, while affording sensible production speeds. Commonly
used peripheral (cutting) speed is in the region of 120-300m/min.
The usable speed depends on the type of blade and material of the
product being cut. Lower cutting speeds are desirable in order to
obtain a longer blade life, while higher speeds are often employed
to utilise the maximum production speed of the mill, when the
minimum cutting time is needed.
In this analysis, the extreme cases of the process will not be
addressed as often presented by other manufacturers. This article is
primarily interested in the standard applications of flying cutoff from
various manufacturers, which cover 60-80 per cent of commonly
employed production mills in various parts of the world.
Graph 1 shows cutting times expressed as possible production
speeds for a mill equipped with flying cold rotary saw. The values in
graph 1 have been compared with values achievable in the actual
production by several factories in the Czech Republic, Slovak
Republic and Germany.
It is evident that using a cold rotary saw limits production capacity of
a mill with increasing diameter and wall thickness of a tube.
Information has been used from a leading Czech tube producer
about the life of the rotary saws and production costs attributable
to the component of a flying saw cutoff module. After taking an
average of the data it is possible to say that for a production line with
the capacity of 26,000t/year (tube and profiles from ST 37 material),
120 replacement rotary saws are likely to be required. Each blade
costs in the region of €150 and can be re-sharpened twenty times.
The total cost of the cutting blades including the sharpening can be
estimated between €38k and €45k per year.
Graph 1