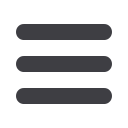

155
M
ay
/J
une
2007
Evaluation of flying shear cutoff
Cutoff by shearing the tube/profile is only used in about 10 per
cent of production mills. The most established company producing
shearing machines is Thermatool, while Italian and Japanese
companies are on the periphery of this sector.
As mentioned, Attl a spol has been involved with this technology
since 1996, and the company’s products have established a high
level of design quality. This is especially the case when it comes
to quality of cut, blade geometry, blade durability and theoretical
understanding of the applied principles.
In Attl’s line of flying shears, the company has focused on production
mills with a maximum production speed of 160m/min, since this
parameter applies to 70-80 per cent of the current production mills.
For shear cutting of square and rectangular profiles Attl have used
one axis type of cut, where the shearing unit can be adjusted ±12°
against the diagonal of the rectangle.
When cutting tubes, Attl selects the two axes type of cut, although
a totally different movement of the blades is used compared with
current producers of cutoff machines.
Attl decided not to select the option of converting the pressing tool
as other machinery makers have. Instead, the company has found
a new way based upon a rotation of the tools against pins and a
large area sliding seat, resulting in a small pressure per unit of area.
This approach has brought with it longevity of contact planes and
the whole cutting unit in general. The life of the cutting unit before a
middle maintenance repair of the sliding planes is 2.5 to 3.5 million
cycles
The tool life of the main cutting blade is standard. Using TiN blade
coating, the main blade life in-between sharpening can be estimated
as 15 to 30 thousand cycles. The life of the slitting blade in Attl
machines is well above average. Common life of Alpha Cut blades
of this type is usually 10 to 15 thousand cycles.
Due to a special design of Attl’s slitting blade, the company has
achieved a life of 120-180 thousand cuts. The life of the cutting
jaws in-between grinding is 80-110 thousand cuts and it is possible
Hot blade saw
Minimal use
No future, very bad quality of the cut surface
Cold rotary saw machine Range of diameters
and wall thicknesses
Remarks
Ø 10-38mm
Very good quality; production speed not effected
thickness 1.2-2.5mm
Ø 16-63.5mm
Very good quality suitable for mill speeds to 80m/min
thickness 1.2-3.5mm
Ø 38-102mm
Good quality; limited production speeds
thickness 1.5-5mm
Ø 76-138mm
Classic concept of cold rotary saw strongly reduces mill output.
thickness 1.5-5mm
Possible solution: Duo; Kvatro
For cutting rectangles using cold rotary saw, similar guidelines apply.
Shearing modules
Range of tube diameters
Remarks
Module SJ 38
Ø 10-38mm
Good quality. Speed of the cutting unit does not restrict output
thickness 1.5-2.5mm
of the production line. Possibility of cutting so called service lengths
1-3m with mill speeds to 60m/min.
Module SJ 63 (76)
Ø 16-63.3mm
Quality sufficient. Speed of the cutting unit does not restrict
thickness 1.5-3.4mm
output of the production line. Possibility of cutting service lengths
lengths 1-3m with mill speeds to 60m/min.
Module SJ 89
Ø 38-89mm
Quality sufficient. Speed of the cutting unit does not restrict
thickness 1.5-4mm
output of the production line. Possibility of cutting service lengths
1-3m with mill speeds to 60m/min.
The shear cutting of tubes with diameters larger than 89mm is not recommended for reasons of high technical costs. The problem can
be effectively solved by using Alda s 138 or Alda s 200 Kvatro cold rotary saw.
Evaluation of parameters for both dividing technologies
›
Figure 1
:
A detail of a sawing unit KS 76x3.4 with flying saw cutoff – Aldas