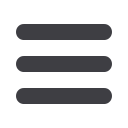

61
M
ay
/J
une
2007
ESTAR: a top ten world
producer
The
managing
company
ESTAR,
established in July 2005, comprises
the Novosibirskiy Metallurgical Works,
Zlatousovskiy
Metallurgical
Works,
Nitvenskiy
Metallurgical
Works,
Volgogradskiy Small Diameter Pipe Plant,
Engelskiy Pipe Plant, Stalnoy profil, Estar,
and Lomprom.
This consolidation of the assets of the
biggest Russian tube companies has
resulted in a top ten entry for ESTAR in the
listing of world producers. Consequently,
ESTAR has gained a competitive edge over
other global producers on the international
market. The volume of exports has trebled
during the last 5 years, with the geography
of exports also expanding from 15 to 68
countries.
Tube research departments have recently
been established at a number of the leading
Russian metallurgical companies, such
as SeverStal, Magnitogors Iron & Steel
Works and others, whose products had
traditionally been geared towards regional
requirements
Advancing technology and
product quality through R&D
The development strategy of the Russian
tube industry is designed to increase
the share of hi-tech, science-intensive,
competitive products in overall tube
production. This target of innovation forms
the manufacturing and technical policy of
all companies.
A number of issues lie at the heart of
these developments, including special
steel grades for pipeline components,
the expansion of product diameter and
wall thickness range, and the introduction
of inside smooth and outside protective
coating for safety during product storage
and transportation. Also of great concern
is the development of new technologies
and scientific-technical documentation, and
machinery design for production of new
pipe-bend and flange size ranges.
The new method of ballast tube production
(concrete solidification) in polyethylene
jacket has recently been undertaken at the
Moscow Experimental Pipeprocurement
Plant, designed for use in construction of oil
and gas pipelines. Two shops – ‘summer’
and ‘winter’ – have been established at
the plant for ballasting steel tubes, with
the technology of ballasting having been
perfected and commercial production of the
ballast tubes already underway.
Considerable research has been conducted
in order to study tube properties with
ballast coating, resulting in developments
and patents. This research includes the
testing of tube specimens for compression
and shift of the ballast coating relative to
the tube body, shift of the jacket relative
to the concrete, and several combinations
of sealing of tube couplings with ballast
coating.
Following the German Lloyd audit of
November 2005, the Certificate of
Qualification of Producer was issued to
Moscow Experimental Pipeprocurement
Plant, with DNV standard certification
almost complete. The products of Moscow
Experimental
Pipeprocurement
Plant
have since been successfully used for
construction of an underwater section of
the Varandeysk oil-loading terminal.
This leading technology enables Russian
tube producers to convert the advanced
system of tube products into the
construction and service support of pipeline
systems.
Strategic long term agreements
for better efficiency
Another priority of the Russian tube
industry is the conclusion of strategic long
term agreements with big metallurgical
companies, particularly the suppliers of
strip and tube billets.
For instance, within the framework of
TMK’s agreements with TMK, the new
steel grades for tube production have
been mastered at Magnitogorsk Iron and
Steel Works. The long term agreements
for quality improvements and sheet metal
product supply have been concluded
between OMK, SeverStal, Magnitogorsk
and UralSteel.
The partnership established between
the ChTPZ Group and EvrazHolding Ltd
has enabled the efficient regulation of
the volume delivery of tube billets. This
agreement was made in order to avoid
potential difficulties in the supply of these
products to the enterprises of the Group,
as well as to reduce delivery costs and
improve the logistics as a whole.
Such agreements are profitable for
enterprises that belong to metallurgical
holdings as they reduce the dependence
of the plants on the instability of the
metal product export market. This leads
to new opportunities and the creation of
considerable areas of consumption within
the home market.
These strict partnership agreements are
therefore designed to guarantee advance
prices and accurate volumes of high-quality
metal deliveries with relevant physical-
mechanical properties.
This consolidation
of the assets of
the biggest Russian
tube companies
has resulted in a
top ten entry for
ESTAR in the listing
of world producers
❱
❱
›
One broad aim of the Russian tube industry is developing technology for an increased product
range of diameter and wall thickness
88