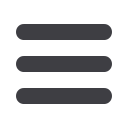

Designersinthetelecommunications,
high-performance
computing,
and medical industries face ever-
changing electrical and mechanical
interconnect requirements. These
industries are driven by increasing
data rates, denser systems, and
shrinking product footprints.
Fortunately for designers in other
sectors,likeindustrial,motioncontrol,
and some military applications,
interconnect requirements do not
change as quickly. Reasons for this
include longer product life cycles,
lighter bandwidth requirements,
and designers do not face constant
pressure to reduce product size,
among other reasons.
Designers in industrial markets are
generally not too concerned with
high-speed interconnects. Ethernet
is usually the maximum bandwidth
requirement.
Many industrial EOEM designers use
the word “rugged” to describe their
board-level interconnect needs.
While “rugged” can mean different
things to different people, it usually
includes the ability to withstand high
shock and vibration applications,
maintain mechanical and electrical
integrity after exposure to harsh
environments and after high mating
cycles, and provide EMI shielding
attributes, to name a few.
Several design elements contribute
to a connector being called “rugged,”
including the contact design, plating,
and insulator design.
INSULATOR DESIGN
Examples of plastic insulator design
features that are popular with
industrial product designers include:
Board locks on connectors that
mechanically lock two PCBs together.
Positive latching systems on
discrete wire and IDC cable systems.
Manually activated latches can
increase unmating force by up to
200%.
Screw downs which secure the
connector mechanically to the
board.
Weld tabs, which significantly
increase shear resistance of the
connector to the PCB.
Dust and water protection are
often a concern; IP ratings such as
IP67 and 68 are frequently required.
Space does not allow us to
discuss the innumerable insulator
design permutations such as
insulator material, heat deflection
temperature, maximum processing
temp, RoHS compliance, or dielectric
INTERCONNECT DESIGN CONSIDERATIONS FOR
INDUSTRIAL APPLICATIONS
Danny Boesing, Samtec
Connectors & Cables
Special Edition
52 l New-Tech Magazine Europe