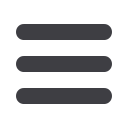

Rugged design features can make
micro pitch interconnects rugged by
incorporating BeCu contacts, weld tabs,
latches, and locks
Contact geometry, orientation, and placement in the
insulator can improve signal integrity performance and
life cycle
strength, among countless other
considerations.
CONTACT DESIGN
We will limit our brief discussion to
contact base materials and design
for rugged applications. Common
base metals include brass, phosphor
bronze, and beryllium copper.
Brass is the least expensive of the
three metals and has excellent
electrical properties. Having said
that, Samtec recommends not using
brass in contacts (receptacles) in a
working beam because it could fail
due to low yield strengths.
Phosphor bronze is stronger than
brass and has better spring
properties. It is excellent for contacts
that have relatively few mating cycles
and low contact flexure.
Beryllium copper (BeCu), while
more expensive than most contact
materials, provides the best
combination of mechanical and
electrical properties. Once formed
and hardened, BeCu will retain its
shape under a wide variety of
conditions.
At Samtec, two contact systems
are most popular for industrial
applications. First is a multi-finger,
heat-treated BeCu system contact.
This is commonly used in 1.27 and
2.00 mm pitch systems. Although
these are micro interconnects
systems, the contact is designed for
rugged environments. For example,
a slot in the tail allows more surface
area for solder adhesion. Also,
connectors with micro tail slots tend
to adhere to the wet solder paste
prior to reflow better than flat leads.
All of this increases the mechanical
strength of the connector to the PCB.
Also notice the slot in the transition
area between the gull-wing tail and
the contact. This slot, while seldom
needed, is designed to prevent
solder wicking. While wicking is rare
in SMT applications because of the
limited amount of solder, if it should
occur, the slot disrupts the capillary
action so the solder does not migrate
into the contact area.
Second is a dual wipe, phosphor
bronze tuning fork design. This design
is popular in rugged applications
because of the contact geometry.
Specifically, the length of the two
mating beams (fingers) allows firm,
consistent normal forces, and is less
likely to take a permanent set after
exposure to numerous cycles.
BANDWIDTH
While system speed is not a concern
for most industrial EOEM designers,
for some it may become a concern
in the future. Industrial Ethernet
is usually the maximum bandwidth
requirement.
Contact systems can be designed
to meet both rugged and higher
bandwidth requirements. One
popular design incorporates BeCu
to maximize spring properties, while
the contact geometry and orientation
in the insulator optimizes signal
integrity. Specifically, the surface
of the contact is milled, creating a
smooth mating surface area instead
of a stamped contact that mates on
a cut edge. This smooth mating
surface reduces the wear tracks on
the contact increasing the durability
and cycle life of the contact system. It
also lowers insertion and withdrawal
forces allowing the connectors to be
zippered when unmating.
The contacts are positioned in the
plastic insulator so the narrow edges
of the pins are parallel to each other.
Connectors & Cables
Special Edition
54 l New-Tech Magazine Europe