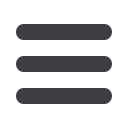

54
Focus on
Scandinavia
September 2012
www.read-eurowire.comS
Nov
3
Spring makers and designers looking
for a high level of fatigue resistance
performance will be interested in
the new duplex stainless steel spring
wire from Sandvik. The new grade,
called Sandvik Springflex™ SF – the SF
stands for Super Fatigue resistant, is
produced using a patented innovation
in processing technology.
Designed to meet the extreme fatigue
performance demands of springs in
common rail fuel injection systems in
motor vehicles, these ‘plunger’ springs
need the necessary strength to carry
high repetitive loads and to last the
lifetime of the motor, without risk of
failure. Space is limited and so the
spring also needs to be small – about 40
grams of wire.
Testing as a compression spring has
confirmed that Sandvik Springflex SF
wire can resist more than 300 million
highly stressed cycles, which has led to
line qualification for the new material
by a major manufacturer of common rail
systems.
In order to meet these demanding
physical requirements and maximise
fatigue performance, Sandvik has
introduced
a
key
manufacturing
innovation. A new, patented process has
been developed, which includes peeling
the hot-rolled wire rod, prior to cold
drawing. This has the effect of reducing
significantly the number of surface
defects, and subsequently improving
fatigue resistance.
The material’s duplex microstructure
means that the beneficial properties of
both austenitic and ferritic structures
are exploited and remain stable
throughout the wire drawing, spring
coiling and heat treatment processes.
Sandvik Springflex SF is, therefore,
less sensitive to crack propagation
than austenitic steels, such as ASTM
302 and 17-7PH steels. The chemical
composition and manufacturing route
mean that ductility remains throughout
the entire production process.
The corrosion properties of duplex
steels are also an advantage and will
benefit the plunger spring application.
There appears to be some evidence
that low quality diesel fuel with high
levels of water content has led to stress
corrosion cracking in common rail
plunger springs.
Common rail fuel injection is designed
to inject fuel into an engine’s
combustion
chamber
under
high
pressure. A common fuel pipeline – the
common rail – supplies the engine’s
fuel injectors. This results in virtually
complete combustion of the fuel with
high-energy conversion and reduced
emissions.
As well as the fatigue resistance
challenge of plunger springs, Sandvik
believes that the new material may find
applications in other markets. Typically,
applications
where
conventional
stainless steels are used but greater
fatigue resistance is required; where
other material grades are used but
better corrosion resistance is required;
or as an alternative to coated surface
springs made from carbon, Cr-Si or
Cr-Si-V steels.
Sandvik Materials Technology –
Sweden
Website
:
www.smt.sandvik.comSpring wire grade sets new standard for
fatigue resistance
▲
▲
A selection of springs made from Sandvik Spring
wire
Photo: bigstockphoto.com –‘Snogebaek, Bornholm, Denmark’Photographer – foto
kate