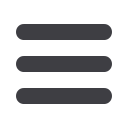

Technology News
www.read-tpt.com86
S
eptember
2012
Dos and don’ts when buying a
second-hand machine
LOWER investment volume, adequate
production capacity – the arguments
for buying a second-hand machine
are obvious. However, in the case of
complex tube bending machines, there
is a whole range of factors determining
the efficiency of using a second-hand
system.
Who buys a car without a test drive
and without knowing its features?
Investment in a second-hand system
resembles this scenario, particularly if
complex tube bending machines from a
niche area are bought without consulting
the original manufacturer. Pipe bending
processing on an industrial scale is a
good example of this: customer-specific
system solutions are used in many
sectors, ensuring high-precision bending
results by means of CNC control,
high performance drives and bending
tools with a complex structure. The
sophisticated plant technology cannot be
simply dismantled and reconstructed to
produce new components in a different
company.
“Detailed questions of component
geometry, material and output quantity
have a decisive impact on the possible
applications of the machine,” said
Hartmut Stöhr, managing director of
bending machine specialist Schwarze-
Robitec. “In our case, the procedure
itself complicates the sale of second-
hand machines by third parties. If one
of our tube bending machines has been
designed for example to process thin-
walled exhaust pipes in mass production,
it might not be suitable for bending thick-
walled high-pressure tubes for plant
construction. Ultimately, whether the
drive concept and machine design can
produce perfect component quality under
the new conditions can be judged only by
one of our specialists.”
“Before buying, it should at least be
ensured that the machine actually works
properly. The control must show no
errors, the mechanics must not be worn
and the machine must be complete
in terms of its components,” said
Schwarze-Robitec’s Bert Zorn. “It must
then be presented in test mode, in order
to be able to clarify for example that all
of the axles still work properly. However,
these criteria are really the absolute
minimum and they are adequate in only
the rarest of cases.”
“There are various options if you
contact us,” explained Jürgen Korte,
authorised representative at Schwarze-
Robitec. “We can look at our records
to see exactly which machine is being
offered. In addition to the delivery
condition and the exact age of the
machine, we can then also provide
statements about whether the machine
has undergone regular maintenance by
the manufacturer.”
Schwarze-Robitec GmbH
– Germany
Email:
sales@schwarze-robitec.comWebsite:
www.schwarze-robitec.comForming rolls manufacturer
THE Atlas brand (DB Engineering) was
formed 60 years ago, and has evolved
to become one of India’s largest tool
equipment manufacturers, currently
with over 600 employees and an annual
turnover of over $20mn. The forming rolls
division was established 25 years ago,
and produces over 24,000 rolls per year.
With specialist knowledge of various
steel grades gained over six decades,
and with an in-house design team, the
company provides a complete one-stop
shop for customers in the cold rolling
industry.
By incorporating world-leading roll
forming software the company is able
to provide technical advice on rolls and
optimisation of production processes.
This approach, combined with ISO-
certified quality standards, has helped
Atlas to become a leading Indian
manufacturer of rolls for the production
of tubes and other roll formed open and
closed sections.
The company can design and
produce tube forming and open section-
forming rolls ranging from 50 to 800mm
in diameter. Before production all roll
designs undergo a simulation and finite
element analysis to achieve ameticulous
final product. All manufacturing is
done in the company’s state-of-the-art
manufacturing workshop with over 15
CNC turning centres.
The ISO-certified in-house heat
treatment facility has a capacity of over
300tn/month, allowing the company to
maintain world-class standards for all of
its products.
Over the last few years the company
has made significant inroads in
the worldwide tube and section
manufacturing industry by supplying to
Australia, North and South Africa, the Far
East, Canada, Russia, the Middle East,
Europe, and various mill OEMs in India.
Atlas Knives (DB Engineering)
– India
Fax: +91 11 26386453
Email:
sales@atlasknives.comWebsite:
www.atlasknives.comA machine in dubious condition