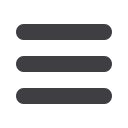

PRODUCT News
46
MODERN MINING
March 2017
Osborn reports that a R27-million order
for a turnkey crushing and screening plant
for a new mine in KwaZulu-Natal reflects
its ability to deliver customised solutions
that are a perfect match to customers’
requirements.
According to Product Sales Manager
Shane Beattie, this new plant features a
unique process designed by Osborn to
minimise fines generation in the produc-
tion of calcite and lime. It has been supplied
by Osborn to Umzimkhulu Industrial
Holdings’ Rossmin opencast limestone
mining operation at Port Shepstone.
“The plant was designed and installed
to only produce two sized products:
80 mm +30 mm and -30 mm + 10 mm. The
-10 mm is a by-product,” Beattie explains.
He says the process is revolutionary in
that a conventional crushing plant would
Osborn provides “unique” solution for opencast operation
The Osborn plant supplied to the Rossmin opencast limestone mining operation.
be a jaw and cone configuration to crush
down to a -80 mm product from a run of
mine (ROM) of 600 mm. “We supplied an
Osborn modular 3042 jaw plant feeding
into an Osborn modular 2340 jaw plant,
then over an Osborn modular 6 x 20 triple
deck screen, splitting the product into
-80 mm +30 mm, -30 mm +10 mm and a
-10 mm +0 mm.
“The primary reason for the two-stage
jaw crushing process is to minimise the
generation of fines (-10 mm),”Beattie elab-
orates, adding that this material is a waste
product.
Beattie says that Osborn’s pioneering
process is more effective than the conven-
tional separation process at other plants,
where all the ROM material is crushed to
-1 mm and smaller, with flotation then
being used to remove the impurities. “This
process requires lots of water and waste
that is more difficult to manage,” he says.
Umzimkhulu and Rossmin will only pro-
cess the high grade material, up to 99 %
calcite. By only feeding the high grade
-80 mm+30 mm to the tertiary/quaternary
plant and, with the next stage being dry,
the plant will produce a higher yield per
ton crushed. “Since this stage is the most
expensive part of the process, by only
crushing the desired calcite, the operation
will be able to dramatically reduce its cost
per ton, and the capacity in this stage is uti-
lised to its fullest potential.”
Beattie says that Osborn’s attention to
detail and commitment to meeting the
client’s needs, together with the compa-
ny’s long-standing reputation for quality
machines and service, led to this signifi-
cant order from Rossmin.
Osborn Engineered Products, tel (+27 11) 820-7600
ELB Engineering signs MOU with Haver & Boecker
ELB Engineering Services (ELB) has signed
a Memorandum of Understanding (MOU)
with Haver & Boecker OHG (HB), from Oelde
Germany, which will allow ELB to provide a
broader service to its existing and future cli-
ents in the sub-Saharan African region.
Haver & Boecker is a world leader in the
cement, chemical, food and beverage and
minerals andminingmarkets with a 130‑year
history. It offers specialised equipment in the
transportation, storing, mixing, filling, pack-
ing, palletising and loading of bulk materials.
Its technology is provided through the fol-
lowing brands: Haver & Boecker, Haver &
Tyler, IBAU Hamburg, Sommer, Behn + Bates,
Feige Filling, Newtec Bag Palletizing and
Haver Automation.
“This partnership with Haver and Boecker
goes a long way in supporting our diversifi-
cation strategy into the FMCG business. We
are very excited about the future opportuni-
ties we can consider together,”says the Chief
Executive of ELB Engineering Services, Dr
Stephen Meijers.
ELB Engineering Services is an inter-
nationally recognised, technology driven,
holistic solutions provider to the mining,
power, port, construction and industrial
sectors.
ELB Engineering Services, tel (+27 11) 772-1400