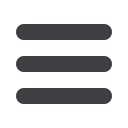

COVER STORY
August 2015
MODERN MINING
21
Michaël Fourie, SPH project manager at
Pilanesberg Platinum Mines, has been on site
since 2011 and has seen a steady ramp up in
their earthmoving and allied machine fleet to
keep pace with increasing mine throughput.
Rising production has also led to a progressive
up-sizing of the capacities on individual earth-
moving units.
At the ROM stockpile, SPH’s Cat fleet of
hydraulic excavators and wheel loaders works
in conjunction with three Metso Mobile LT120
jaw crushers. All blasted in-pit material is
transported to a ROM stockpile area by a sepa-
rate load and haul contractor. A total of around
300 000 tonnes of ore (Merensky Footwall
Pseudo Reef (Silicate) and UG2) is processed
and hauled for the client, Pilanesberg Platinum
Mines, on average per month.
“Two thirds of our tonnage is Silicate ore,”
Fourie explains. Allied materials handling
chiefly comprises UG2 reef. These are relatively
high Specific Gravity (SG) materials. With
these SGs all machines work physically hard
and need to be optimally configured for their
assigned tasks to ensure predicted availability
Above:
The Cat 340D2 L is
manufactured at Caterpil-
lar’s Xuzhou factory in China
for worldwide distribution.
Above left:
In the fore-
ground, a Cat 320D L hy-
draulic excavator, equipped
with a hydraulic hammer,
breaks up oversize material,
which will then be fed into
one of SPH’s Metso LT120
mobile jaw crushers.
goals are met, and scheduled maintenance
stays within budget.
SPH deploys a Cat 980H wheel loader to
handle any oversize. Cat 320D L excavators
equipped with hydraulic hammers then break
up larger ‘boulders’ for subsequent feeding into
the Metso Mobile jaw crushers.
Cat 966H units are utilised for general pre-
and post-crushed materials handling stockpile
management. The Cat 980H has recorded close
to 22 000 hours from new since being on site
with only minor interventions, and SPH plans
to run the machine to 25 000 hours before
reviewing component rebuild requirements.
Meanwhile, SPH’s Cat 966H units on site
have each achieved around 12 000 hours; a new
Cat 966H joined the fleet in July 2015 bringing
the total to four. The new unit comes equipped
with a larger counterweight and a 4 m³ bucket.
On the critical path to the crusher, mate-
rial loading is carried out by 40 and 50 tonne
class hydraulic excavators. These include a Cat
340D L, which is one of the key loading tools,
and comfortably keeps pace with the LT120’s
volume throughput. This typically averages