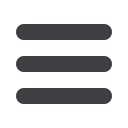

August 2015
MODERN MINING
45
PROCESSING
Two large Longi-Multotec
vertical ring WHIMS
machines, each capable of
processing up to 150 tons
per hour of solids.
intensity multiplied by the gra-
dient is called the force factor
and is responsible for separating
minerals. The Longi-Multotec
WHIMS machines typically
have a force factor of 200 mil-
lion Gauss
2
/mm and this is a
vastly significant difference
when compared to a traditional
low intensity wet drum mag-
netic separator, which has only
20 000 Gauss
2
/mm.
“Trials indicate that the
WHIMS can recover particles
down to a fraction size as
small as 5 micron, a charac-
teristic that is attributed to the
exceptionally high force fac-
tor. Particle sizes as small as
80 % passing 30 microns have
been recovered. To put this in
perspective, this particle size
is finer than the diameter of a
40 micron human hair,” Slabbert points out.
In some areas PGM ore has a head grade of
between 1,4 and 2,5 mg/t and the tailings that
have been processed in the test work to date
have had a head grade of 0,8 to 1,5 mg/t. This
is significant given the fact that through the
conventional flotation process it is not eco-
nomically feasible to attempt to float the tails
again if below 3 mg/t.
With the Longi-Multotec WHIMS, the
chrome is removed so that a saleable product is
recovered and, furthermore, the PGM grades are
upgraded to above 3 mg/t. It then becomes eco-
nomically feasible to refloat through existing
capital infrastructure. This presents advantages
over and above the costs associated with min-
ing and the comminution process, which may
well contribute to almost 60 % of the opera-
tional costs of a plant.
A major benefit of the Longi-Multotec
WHIMS machine is that once the test work
data has been verified the machine can be
upscaled to a capacity of up to 300 t/h of sol-
ids (or 1 000 m
3
/h of slurry) through a single
machine. Multotec is able to supply vertical
ring WHIMS machine sizes in the range of 1 t/h
up to 300 t/h.
“This high capacity completely overshadows
the much lower maximum capacity of 30 t/h
that a horizontal ring WHIMS can achieve.
Extensive tests have shown chrome grades of
43,8 % are readily achieved with the vertical
ring WHIMS, which is significantly higher than
the industry standard of 42 %, and indicates
that the percentage grade achievable on full
scale plants in all likelihood will be higher,”
says Slabbert.
In addition to its proven increased recovery
capacity, the Longi-Multotec WHIMS machine
provides industry with a number of attrac-
tive benefits that are said to include ease of
maintenance and operator friendliness, lower
operating costs, environmentally friendly
equipment operation and easy and reliable pro-
cess performance.
The vertical ring WHIMS makes use of only
one coil, resulting in savings on electrical
infrastructure and electrical consumption for
decreased capital cost of ownership and opera-
tional costs. By feeding into the slurry feedbox
instead of directly onto the matrix, there is a
better tolerance of feed fluctuation without the
separation process being affected. Control of the
machine is also improved and it is more reli-
able resulting in better separation consistency.
“Pulsation allows a cleaner product to be
produced, with better upgrade ratios achieved
under variable and controlled conditions. The
matrix boxes in the rotor can be changed out in
situ and individually after wear or damage to a
box, eliminating a total rotor change out. This,
again, provides significant operational savings
and ease of maintenance,” adds Slabbert.
Slabbert explains that most of the test work
has been done repeatedly using the Multotec
vertical ring WHIMS on different samples and
different seams of UG2, LG6 and MG tailings
derived from Western Limb of the Bushveld
Complex material, with some tests having been
conducted on the Eastern Limb material.
“Trials indicate
that the WHIMS
can recover
particles down
to a fraction
size as small as
5 micron ... .”
Willem Slabbert,
Multotec Process
Equipment