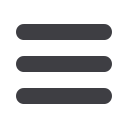

November 2015
and flying shuttle system – all fully
automated – as well as a hot water
heating system for accelerated curing
of the products. Even the cranes were
part of this extensive order and were
shipped from Europe.
Following a study of Perse’s re-
quirements, the necessary technical
equipment was specified for a new
hollow core slab plant to be placed
beside the existing hall. Included in
the offer was a detailed investment
analysis that showed that a new
weiler production system, using a
similar area and material inputs as
thewet-cast hall, could produce three
times the volumes, with a direct cost
saving of 28-40% per m² of precast
production.
Production cycle times could be
reduced to 6 - 8 hours total per bed;
one hour to extrude slabs and 5 - 7
hours to cure, cut and lift sections.
With four production beds, each
120 metres long, the beds can pro-
duce twice a day, so that the daily
nominal capacity would be 1 680
m² of flooring or walls, compared
with the existing wet-casting system
producing 560 m² with eight produc-
tion beds. By adding four additional
production beds to the new weiler
productionhall, nominal capacity can
be increased to 3 360 m² of floors or
walls per 24 hour period.
Following quality and volume
requirements, low unit production
cost was a critical objective for Perse
directors. This requirement was met
by using the weiler extruder (MAX-
truder) for slab/panel production.
The extruder uses a dual vibration
compaction system to compact a dry
concrete mix with low cement con-
tent (water cement ratio 0.32 approx.)
and no admixtures, which results in
elevated final compressive strengths
averaging 75 MPa (750 kg/cm²).
Higher strengths allow for lighter
and stronger elements, a key feature
of weiler slab and panel precast ele-
ments. Combining lower concrete
costs with lighter (lower concrete
volumes) sections, means weiler
extruded slabs/panels cost 28% -
40% less per m² than wet-cast slabs/
panels.
For the new factory layout, weiler
design engineers were faced with
challenges:
•
Integration of the new factory
alongside an existing production
hall and systems without disrup-
tions to processes
•
Designing-in work and material
flows to separate the rawmaterial
storage andmixing areas, from fin-
ishedproduct, storage and loading
areas
•
Providing timely, mixed concrete
delivery to precast production up
to 200metres fromthe batchmixer
station
•
Ensuring that future expansions,
new production additions would
be easy and be served by the same
infrastructure
A critical part of the layout challenge
was resolved with the use of an au-
tomated batch mixer station placed
in the existing material storage and
mixing area, delivering concrete by
flying shuttle on elevated rails, in-
cluding curved sections, to the new
hall production area.
weiler considers this new ad-
vanced extruder factory an important
milestone for Perse and is proud to
have been the chosen supplier.
For add i t i ona l i n format i on
email:
info@weiler.netor visit
www.weiler.net■
technology plant