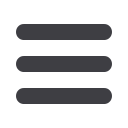

News
Technology
September 2015
35
www.read-eurowire.comWhile the extruder is the melt supply device in most extrusion
processes, the basic design has not evolved much over the last
few years. Its purpose is to supply molten material at a constant
melt temperature and at a constant volumetric rate.
The typical extruder is made up of three geometric sections:
The feed section or solids conveying, the transition or melting
section, and the metering or pumping section. Frigeco has
redesigned a number of areas on the Frigeco extruder:
• Feeding zone
• Extruder barrel and screw profile
• Thermoregulation
• Stable and reactive electronics
• Increased output and lower energy consumption
The actual melting takes place in the feeding zone. Most plastics
are poor conductors of heat and are melted by shearing the
material against the barrel rather than by heat conduction.
Consistent flow of material into the extruder barrel is obtained
by controlling the temperature of the feed throat.
However, you cannot rely on plant water supply which can vary
from 38ºF (3ºC) in the winter to 75ºF (24ºC) in the summer. These
fluctuations in temperature will affect melt temperature and
cause product variations.
Therefore, controlling the temperature of the feed throat is
essential to constant solids conveying. The Frigeco grooved
feed throat, integral cooling jacket and closed loop water
temperature control circuit provide a constant feeding zone
temperature. The next section is the transition zone, where a
large amount of heat will be generated.
Much of the heat necessary to plasticise the material comes from
the rotation of the screw. The faster the screw rotates, the higher
the surface speed of the screw, the greater amount of shear in
the material and therefore an increase in melt temperature.
The combination of rotational speed, adequate cooling and
accurate temperature control will keep the shear rate down and
prevent localised overheating.
It is in this area that Frigeco engineers have done the most
extensive research and redesign.
Frigeco – Italy
Website
:
www.frigeco.comFrigeco engineers redesign extruders
▲
▲
Redesign work has been extensive from Frigeco