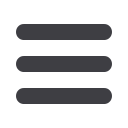

Transatlantic cable
September 2015
31
www.read-eurowire.comthe pressures of the Townsend but on a much smaller scale
and using completely di erent mechanics. Mathematical
calculations con rm that they essentially test the same types
of strain.
Mr Maroney’s materials advisors will be taking other measures,
both mechanical and modelled, to tease out the cause of the
failures.
At the same time, the anchor rods are not the sole problem
with the Bay Bridge. Rods under the main tower are threatened
by water corrosion. There are misaligned deck sections. And
inspections have turned up substandard welds in the tower and
roads.
But right now, Mr Stockton wrote, the main focus is on the
32 anchor rods in the eastern suspension pile “and what caused
them to corrode where others did not.”
Famous for its canals, Amsterdam is set to
welcome a related attraction:
the rst-ever 3D-printed steel bridge
Another highly advanced bridge – the world’s rst to be
constructed by means of 3D-printing methods – is attracting
attention in the city of Amsterdam.
In the rst large-scale test of the technology, a Dutch start-up
plans to employ robotic printers to weld the structure even as it
inches across a canal.
This bridge has none of the problems currently experienced in
San Francisco. But then, it was still in pre-production in advance
of a September demonstration when the engineering company
MX3D issued this statement: using robotic printers “that can
‘draw’ steel structures in 3D, we will print a pedestrian bridge
over water in the centre of Amsterdam.”
In a rst large-scale deployment of the technology, robotic-arm
printers will “walk” across the canal, essentially printing their
own support structure as they progress. The robotic arms will
heat the steel to a searing 2,700º. Fahrenheit to weld the bridge
– a sophisticated computer-generated design – drop-by-drop.
“The underlying principle is very simple,” the bridge’s designer
Joris Laarman told Agence France-Presse (16
th
June). “We have
connected an advanced welding machine to an industrial robot
arm.”
The technique could, the company said, become standard on
construction sites, especially those involving dangerous tasks
on high buildings. It also obviates the need for sca olding as
the robot arms will support themselves with the very structure
they print.
It is obviously not a rapid- re method; nor can the permissions
process be rushed. While Amsterdam City Council spokeswoman
Charlene Verweij said the Dutch capital was supporting the
project, in June there was still uncertainty about a speci c site
for the bridge, which the designers hope will be completed by
mid-2017.
“I strongly believe in the future of digital manufacturing and
local production,” said Mr Laarman, taking the long view.
“This bridge can show how 3D-printing has nally entered
the world of large-scale functional objects and sustainable
materials.” (The Guardian, 16
th
June)
He added: “It’s a new form of craftsmanship.”
A concern about 3D-printing – or additive manufacturing, as it is
also known – is whether the properties of 3D-printed materials
are equal to those of conventional manufacture.
Iain Todd of the Australian news service
The Conversation
reported that, generally speaking, 3D-printed components can
be comparable to their traditionally produced equivalents.
Beginning with the prototyping of objects through the various
stages of development, the method has in fact been in use since
the 1980s.
Today, 3D-printed surgical devices – hip implants, for example –
are not uncommon. And 3D-printed parts have been a feature
of Formula One racing cars and military aircraft for years,
performing very well.
In reference to the canal bridge in Amsterdam, Mr Todd wrote
(19
th
June): “What we are seeing now is that the technology is
becoming more mainstream – and that change is helping drive
a huge explosion of creative thought about how, and where, we
make things.”
Automotive
In the wake of fatalities tied to General
Motors cars, ‘a seminal shift’ in how US
regulators will deal with automakers
“From Day One I said, isn’t NHTSA just as guilty as General
Motors is? It’s terri c they are nally owning up to their mistakes.”
The stepfather of a victim of one of the 109 fatal accidents
linked to a defective ignition switch in General Motors cars was
referring to the National Highway Tra c Safety Administration.
In June, after more than a year of castigating the automaker, the
NHTSA, a unit of the US Department of Transportation (DOT),
had acknowledged its own role in the gravest safety crisis in
GM’s history.
Two internal DOT reports identi ed a series of failings by the
NHTSA that allowed millions of faulty GM cars to go unrepaired
for more than a decade. The ignition switches could suddenly
turn o , stalling the engine and disabling the airbags.
As noted by
New York Times
reporters Bill Vlasic and Rebecca
R Ruizjune, while the reports still xed blame for the crashes
squarely on GM, the nation’s largest automaker, they also
included an unusually blunt catalogue of mistakes made by its
regulators. (“Safety Agency Admits Missing Clues to GM Ignition
Defects,” 5
th
June)
The agency admitted having ignored signs of the defect, and
failing to bring its full authority to bear on GM. In a conference
call with reporters, transportation secretary Anthony Foxx said
NHTSA is now revising its investigative procedures, stepping
up e orts to obtain safety data from automakers, and creating
an oversight team of outside experts to help put the changes
into e ect.
For his part, the NHTSA administrator, Mark R Rosekind,
in the job only since December, had already adopted a
more aggressive stance toward the auto industry, pushing
in particular for quicker responses on continuing safety
issues at Fiat Chrysler Automobiles and the Japanese airbag
manufacturer Takata.