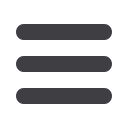

The trip point tolerance (i.e. potential trip point error) may be established fromapublished safety
specification identifying the appropriate tolerance, or itmay be calculated fromequipment
performance specifications. This is not necessarily a straightforwardmatter however, a rigorous
calculationmust combine accuracy and drift specifications of the systemcomponents togetherwith
the calibration interval, and include installation effects and pertinent influence quantities such as
equipment operating temperature and process operating conditions; this is beyond the scope of the
present article. Note that some safety specification tolerancesmight well be an ordermagnitude
greater than those simply identified by the more usual performance (accuracy) specifications. The
performance and calibration of instrumentation systems is often identified using a95% confidence
level correspondingwith two standard deviations of anormal distribution. This implies a1 in 40
chance of a dangerous out of tolerance value fromthis consideration alone. This is not consistent
with SIL performance requirements. It is here suggested that a tolerance established frompublished
specifications (and incorporating drift, installation effects and influencequantities) should therefore
typically be expanded by at least a factor two. (Giving a tolerance at approximately 99.994%
confidence)
The ultimate requirement is that the SIF response time should not exceed the PSTminus the
potential delay due to trip point error.
= −
A more refined rule-of-thumb as a design target would be to say that that the SIF response time
should be nomore than 50% of the maximumallowable.
Without this refinement it is conceivable that adesign could appear to be satisfactorywith an SRT of
less than 50% of the PST, but potentially unsafe in that the trip point tolerance couldmean an
additional potential delay of more than the remaining PST. The 50% design rule makes allowance for
increased SIF response times in the installed system. There is nothing substantiating the 50% figure
however, it represents a judgement of what is a prudent allowance . If the design is found to breach
the above rule-of-thumb (or is otherwise considered to be possibly insufficiently robust in terms of
the timings), the options are:
Engineer a reduced SIF response time
Engineer a reduced trip point tolerance
Considerwhether the values for the process limit and/or approach speedmay be revised
Change the trip setting to increase the margin fromthe process limit
Use more rigour in the analysis to demonstrate that the
guaranteed
trip execution time (i.e.
that for which the declared failurerate used in the probability of failure on demand
calculation is valid) is less than the PST.
Conclusion
The widely employed rule-of-thumb that SIF response time should be less than 50%of process safety
time is potentially deficient in that it does not take account of a number of subtleties in the
characteristics of trips relating to continuous process variables; in particular the uncertainty in trip