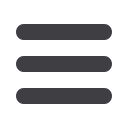

Functional Safety 2014
4
th
– 5
th
November 2014
Copyright © 2014 by Cenbee Bullock PFS Consulting Ltd
Page 7 of 14
identifies the probability of dangerous systematic failures on demand (PFDsys) of a process plant and
the probability (P) of systematic failures caused by human errors including faults in design, installation,
proof tests and in by-pass mode.
PFDavg = ƩPFDsensor + ƩPFDlogic solver + ƩPFDfinal element + ƩPFDpower supply + ƩPFDsystematic failures
Where PFDsystematic failure = PFDsys-process plant + Psys-human error
And Psys-human error = Pdesign error + Pinstallation + Pproof test error + Pbypassed
Unfortunately, it is not easy to model systematic failures accurately and they are rarely included in the
SIL verificationmodelling. It is due to the difficulties in obtaining the failure rates and in most instances,
systematic failures can be very specific to a particular operation and process plant.
In the 2
nd
edition of IEC61508, there are techniques and measures to control systematic failures under
various stress conditions. Part 2 table A.15 to A.17 recommends some techniques and measures to
demonstrate the systematic capability.
How to minimise systematic failures caused by human error?
Human error is one of main causes of systematic failures. If we refer to some of the research and
studies, human mistakes and errors can occur throughout all the phases of the safety lifecycle.
The Swiss Cheese Model can be used to represent the safety lifecycle activities, with the holes
representing human errors in the various phases (slices) of the activities. (Design, development and
verification of Programmable Electronic Systems will be discussed in more detail in a later section).
Some of the errors and mistakes may seem to be insignificant: for example, assuming competently
trained duty operators would be available to cover all operating hours and are all fully appraised of
the actions required when responding to safety critical alarms.; or, designing a safety instrumented
function with SIL 2 requirement without understanding the implication of no segregation or
independence between the basic process control system and the SIL rated system; or, through
ignorance of environmental influences, installing sensitive electronic devices next to high voltage
equipment. Unless these seemingly insignificant assumptions are addressed, and resolution is
overseen and supported by the management team, these assumptions could lead to a major failure.