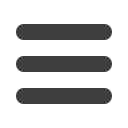

Wire & Cable ASIA – September/October 2007
57
Wire & Cable ASIA – November/Decem 11
In order to route vertical cables efficiently and
unobtrusively inside buildings, Corning’s design efforts for
this product focused on smaller diameter and more flexible
units leading to FRNC micromodule cables as shown in
Figure 3
.
An additional advantage of this cable is the extremely
small bend enabled by ClearCurve
®
[2]
fibre that allows
discreet storage of fibre in the building, either for tether or
for excess pigtails lengths.
The flexibility and the small outer dimensions of the riser
cable assembly ensure the very easy installation of the
cable and routing through the wall or on the various levels
of the building.
2 Installation conditions
One of the most critical issues
related to cable installation is
pulling through the vertical duct
already installed in MDUs (
Figure 2
).
The following tests were performed
to simulate installation conditions
and define installation limits
of the cables in terms of duct
congestion. The installation pro-
cess was simulated for several
duct diameters and shapes both
with and without copper cables
already installed. Additionally, duct
misalignment and gap size shown
in
Figure 4
were considered.
Tests were performed for 3m duct
pipes with different dimensions.
This simulates typical 3m distances between floors in the
MDU building.
Each cable was pulled three times for every configuration.
Figure 5
shows the pulling force for a 6x4 configuration
measured for three duct with various inner diameters (ID)
and with different filling ratios.
Results showed that the most important factor is
the number of riser tap points, which will be pulled
simultaneously through the duct. However, the pulling
force for different fill ratios depends also on copper
twisted pairs arranged inside the duct.
The total pulling force during installation should not exceed
500N. Based on duct size, fill ratio and misalignment data,
the maximum number of tap points pulled simultaneously
can be calculated as:
Where, F# is number of floors, MF is misalignment force
and PF is pulling force.
3 Reliability
The qualification test plan was a variation of the GR-3122
specification, modified to reflect indoor usage.
Test samples were prepared in the most common
configurations; 6 x 4 – 6 tap points, each with 4f, 12 x 4
– 12 tap points, each with 4f and 12 x 8 – 12 tap points,
each with 8f.
For such a set of samples the following tests were
performed: thermal aging, thermal and humidity cycling,
sheath retention, cable flexing, compression, assembly
installation, pulling through ducts, cable pulling and
straight and 90° tether pull. All tested samples passed
both environmental and mechanical tests without any
issues.
As an example for the extensive test programme the
sheath retention test set-up is presented in
Figure 6
.
❍
❍
Figure 6
:
Sheath retention setup
Electronics
35%
Passive
components
15%
Labour
50%
Max. # of tap points
Mandrel
15x
cable
diameter
Basket
grip
Cable held
firmly in
place
To optical
test equipment
Cable
Load
Over-
mold
❍
❍
Figure 7
:
Typical first installed cost
[3]