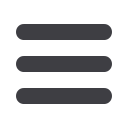

Industry
News
16
Wire & Cable ASIA – March/April 2007
2006 success for Boxy
It has been an important and successful
year for Boxy, of Remedello, Italy.
From its plants in Brescia, Italy, and
Slovakia, Boxy produces reels for
copper cables, welding wire and metal
cores for tyres.
With a turnover in 2005 of €7.9 million
– up €1.6 million from 2004 – a further
leap to €11.5 million is expected for
2006.
The company also has two chief
executives with the addition of Stefano
Sorlini, joining Mario Ferrari in the
boardroom.
With 40 employees and the technical
office in Remedello, a staff of 90 in
Slovakia and a sales office and after-
sale service at their subsidiary
Mossberg Reel for the US market,
Boxy has also started improvements at
its Brescia headquarters, renovating
machines and further developing the
automation side of the business.
This €1 million investment is aimed at
the core business of reel production
and increasing production of lifting
units, tilting units and accessories.
Since 1969, Boxy has firmly established
themselves on the international market.
The production cycle is regulated from
procedures CAD-CAM which control
the parameters of process and quality.
The main models produced are:
BTE
: machined and electronically
balanced for speeds up to 50m/s for
wire and multi-wire
NA
: with double wall flanges, machined
and electronically balanced for speeds
up to 50m/sec
BST
: in pressed steel, for strands and
cables
BMP and BAL
: in large dimension for
cables and ropes
BFP
: with reinforced double wall
flanges, machined and balanced for
steel wire drawing and annealing
Among the main models presented by
Boxy, the take–apart reel ‘Koiler’ has a
high demand in the market. The
mechanism of this model allows the
lower flange of the reel to be
unfastened and the drum to be closed
automatically, hooking and lifting
with the right accessories, without
having to unscrew or unfasten except
for the safety device.
Boxy SpA – Italy
Fax
: +39 030 957 244
:
boxy@boxy.comWebsite
:
www.boxy.comDoubles capacity
Daikin have doubled their capacity
after the successful start-up of their
ETFE expansion in Decatur, Alabama.
The expansion demonstrates the
company’s commitment as the largest
US manufacturer of Ethylene –
Tetrafluroethylene copolymer (ETFE).
Daikin America Inc – USA
Fax
: +1 845 365 9598
:
customer.service@daikin-america.comWebsite
:
www.daikin-america.comAllied’s new site
A faster and more convenient service is being offered for customers in the
Midwestern and Western states after the opening of a stocking facility for
Allied Wire and Cable in Elkhorn, Wisconsin, USA.
The extra stocking room frees up space for more products at the international
headquarters in Pennsylvania and other Allied offices.
All locations, including Wisconsin, have added 1283, 1284 Extra Flexible MTW/
TEW (Bare Copper) to their inventory. The Flex MTW, which is used for a wide
variety of applications, meets UL requirements and will be stocked in large reels.
“At Allied, we believe the customer comes first and we always strive to make
that evident. The stocking facility and new product line help us offer the best
possible service to every customer,” said Hans Nelson, manager of the
Wisconsin branch.
Allied Wire & Cable – USA
Fax
: +1 800 615 WIRE (9473)
:
info@awcwire.com•
Website
:
www.awcwire.comImproving lubrication
and clearning
The new GPS/PDH wire re-coating system greatly
improves the present state of both wire lubrication
and in-line wire cleaning. The system enables
high-speed ‘frictionless’ drawing, benefiting from
the wire dry re-coating in intermediate drafts with
completely water-soluble sodium lubricants.
Full film coatings are achieved in a wide variety of
selections from ultra thin (plating wire) through to
a strongly adherent hard coat (spring wire, cold
heading wire, etc). This allows substantial cost
savings in drawing applications including spring wire,
high-tensile rope wire, bead wire, PC strand wire,
stainless steel wire, galvanised H/C or L/C wire,
AL-cladded wire, plating wire, CO
2
welding wire,
colleted nail wire and cold heading wire. The GPS/
PDH system powerful multi-action capabilities permit
in-line wire cleaning in the following:
Dry application:
The unit is installed in the last drafts
operating with a specific, completely water-soluble
lubrication. This forms a consistent pressure pad
all around the wire which is continuously renewed
in closed circuit and creates a microfilm residual
which can be easily cleaned by simple washing.
In this application the GPS/PDH unit simultaneously
performs surface cleaning and polishing effect in
a single run.
Wet application:
The GPS/PDH unit is installed in
the last draft, operating with a paste in a continuous in
and out motion, in closed circuit pressure lubrication,
self generated by the unit itself. A light draft performs
cleaning, polishing and provides a reflective wire
appearance in a single run.
Decalub – France
Fax
: +33 1 60 20 20 21
:
info@decalub.comWebsite
:
www.decalub.com