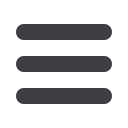

2 15
BEST
PR
O
JECTS
50
CONSTRUCTION WORLD
DECEMBER
2015
Specialist Contractors or Suppliers
B
Project information
• Company entering: Aveng Grinaker-LTA
• Project start date: 28 May 2014
• Project end date: 28 February 2016
• Client: Sasol Synfuels
• Main contractor: Aveng Grinaker-LTA
• Project manager: Aveng Grinaker-LTA
• Consulting engineer: Wynand Louw
& Associates
• Project value: R66 037 396,82
Repeat client, Sasol Group Technolo-
gies, required urgent repairs to their
eight rapidly dilapidating concrete
process water cooling water towers.
The scope would entail the removal of
spalled concrete, replacing of reinforcing,
reinstating with structural grout and sealing
of the entire structure with polyurethane
coatings. Sasol engaged the services of
Sasol Process Water
Cooling Tower
Aveng Grinaker-LTA’s specialist concrete
repairs team to carry out the repairs to the
first tower in need of the most repairs, with
the possibility of more towers being awarded
at a later stage.
Providing safe access to the top of the
tower and work face provided the most
complicate challenge – especially with the
complex shape of the structure. The Process
Water Cooling Towers at Sasol Secunda are
140 m high, 65 m in diameter at the top and
105 m at the bottom.
The structural raking columns take up
the bottom 20 m and prop up the structure.
Access is provided by a means of Alimak and
24 Temporary Suspended Platforms. These
comprise of 16 x 8 m wide working platforms
and 8 x 4 m wide shuttle platforms. Alimak is
installed to the profile of the Process Water
Cooling Tower.
The vertical level was controlled with
a theodolite. Mast sections were running
parallel to the tower surface and anchored
to the concrete. Initially the anchors were
chemical anchors which changed over to
express anchors due to the 150 mm thick-
ness of the wall. The profile against the
tower was achieved by installing spacers
to the mast sections to allow the sections
to curve. This is only done every second
section. Special brackets were designed to
accommodate the walking platform on the
top rim of the cooling tower.
A monorail section is installed with
brackets to allow a temporary platform to
suspend from the brackets while still being
able to transverse horizontally. The move-
ments (vertically as well as horizontally) of
the temporary suspended platforms (TSPs)
were the main concern of the project as this
is where the most time would be lost.
As the project kicked off into the
construction phase, extra methods were
adopted and innovated to achieve a higher
efficiency. These included a trap door design
to allow the team to enter from the top
platform to reduce the lost time of access
to the system. This eliminated the time lost
by using the shuttle platforms to access the
work area from ground level.
Special
Mention