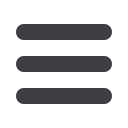

2 15
BEST
PR
O
JECTS
52
CONSTRUCTION WORLD
DECEMBER
2015
Specialist Contractors or Suppliers
B
With the University of Pretoria contin-
uing to grow and more and more
students coming from outside
Pretoria, student accommodation is
very scarce. Ellinas Developers saw an
opportunity here and successfully leased
the planned ‘Hatfield Studios’ to the Univer-
sity and a very ambitious build commenced
in November 2013, occupation date
December 2014.
Project information
• Name of company entering: PERI Formwork
& Scaffolding Engineering
• Project start date: 8 July 2013
• Project end date: December 2014
• Client: Feenstra Group
• Project team: Feenstra Group
• Main contractor: Basil Read
• Architect: Boogertman + Partners
• Project manager: Feenstra Group
• Quantity surveyor: DelQS
• Consulting engineer: DG Consulting
Engineers
Hatfield Studios
Generally a building will have two to
three shafts for access, one for lift access,
and one or two for stair/emergency exit.
Hatfield Studios which consisted of a large
parking basement and two towers of rooms,
had a grand total of 12 shafts.
Inaddition to this, the east andwestwalls
of the basement and towers were off-shutter
concrete feature walls. The progress of a
shaft or feature wall always determines the
progress of the whole project.
Cranage was always going to be a
critical resource and with the construc-
tion site having a relatively small footprint,
the main contractor decided on only two
tower cranes.
With each shaft and feature wall
requiring at least four hours of crane time, 56
crane hours would be consumed every two
weeks on the shafts and feature walls alone
to meet the ambitious programme.
Also, the towers were designed with
structural internal walls requiring crane
lifting of gang-formed shutters there too.
The advantage of this design is that
the floors are very modular which is perfect
for custom made table formwork.
The initial plan from the formwork
supplier was to utilise 16 m
2
tables and crane
them into position, one by one.
It soon became apparent that there
would not be sufficient surplus crane
capacity to move flooring formwork.
The tables were replaced with the light
man-handable Skydeck 1,125 m
2
panel
which could be carried from floor to floor.
The heaviest part of the Skydeck system, the
2,25 m long main beam, weighs just 15,5 kg.
Eight hour days quickly turned into
16 hour days with self-compacting concrete
being poured late into the night. Although it
was a very ambitious programme, accuracy
was paramount as the main contractor had
opted for a pre-manufactured modular bath-
room requiring tolerances of millimeters to
fit into the rooms.
Errors did occur and critical remedial
work had to take place including breaking
down an interior wall, propping the floors
and then recasting the walls from the bottom
of the shutters with self levelling concrete
and a special pump/shutter adaptor.
Labour took strain with the long
hours, there was a month-long steel strike
during winter, but the University took
reasonable occupation in the middle of
December 2014.
Photos by Oliver Karstel