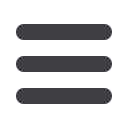

6
SAIWmember profile: Transnet Engineering
AFRICAN FUSION
June 2016
T
he contract between Bombardier
Transportation South Africa and
Transnet Freight Rail (TFR) for 240
Bombardier TRAXX Africa locomotives
is part of the largest locomotive supply
project in South Africa’s history, with
overall orders for 599 electric and 465
diesel locomotives from four different
suppliers. TFR will use the 240 TRAXX
Africa dual-voltage electric locomotives
– valued at approximately R13-billion
based on the original list price and
exchange rates –for its general freight
business.
As part of the localisation require-
ments, the fabrication of 480 bogies
required by TFR for the locomotives
has now begun at the Durban facilities
of Transnet Engineering. Before doing
so, however, EN 15085 certification for
themanufacture of railway vehicles and
components was required.
EN 15085 applies to the construc-
tion, manufacturing and testing of weld-
ed rail vehicles and their components.
“This is the European railway engineer-
ing standard and, for Bombardier, as a
European OEM, it is a non-negotiable
quality standard,” says Baloyi. “For us,
therefore, all of the fabricated bogies
that we are contracted to build are re-
quired to be welded in accordance with
EN 15085,” he adds.
The localisationof the railway indus-
try cannot be achieved unlessmanufac-
turers of vehicles and components are
successfully audited and certified to this
code. As TE in Durban we are mandated
to comply with EN 15085 for the 1064
project. We cannot comment about the
certification requirements of other fab-
rication companies, except to confirm
that it was required as a pre-condition
that we are EN 15085 certified.”
In addition, before a fabricator can
be certified for manufacturing welded
railway vehicles, it has to already be
operating according to ISO 3834, quality
Transnet Engineering:
the first CL 1-certified
rail fabricator in Africa
Transnet Engineering’s executive manager of R&D, Collin Moopanar; welding engineer, Dhurusha
Govender; and the company’s internationally certified welding engineer, Rodwell Baloyi (IWE).
African Fusion
visits Transnet Engineering’s EN 15085-certified Durban facility and talks
to welding engineers, Rodwell Baloyi (IWE) and Dhurusha Govender, along with Collin
Moopanar, the executive manager of R&D mechanical.
requirements for fusion welding of me-
tallicmaterials. “And the railway require-
ments are different again. EN 15085 is a
different andmore rigorous standard to
any of those we have previously imple-
mented,” adds Govender.
Transnet Engineering’s Durban
facility has been accredited to ISO 3834
Part 2. Then, late last year, the facility
became the first fabricator in the South-
ern Hemisphere to be certified to the
highest level (Certification Level 1 or
CL 1) of EN/ISO 15085-2. This certifica-
tion level is essential for any new build,
conversion or repair of railway vehicles
or components, including: bogies and
under frames; vehicle bodies; draw
and buffing gear; supporting frames;
wheel-setmountings, axle boxes, spring
supports, shock absorbers and vibration
dampers; brake equipment; supporting
frames for heavy duty vehicles; welded
bolsters; fuel tanks; and any safety criti-
cal welded component.
“Aligning to EN 15085 involves a
mind-set shift, mainly due to person-
nel changes,” reveals Baloyi. “While
ISO 3834 does not specifically require a
welding engineer as part of the fabrica-
tion team, for example, EN 15085 insists
that all weldingoperations areunder the
direct control of an internationally certi-
fied welding engineer (IWE),” he adds.
Baloyi and Govender are both qualified
welding engineers, while Baloyi also
holds the IWE qualification, as required.
“At any given time, vehicle OEMs
such as Bombardier or CNR need to be
1
2