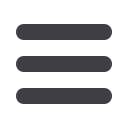

33
CONSTRUCTION WORLD
APRIL
2016
Vitreous enamel steel cladding supplied by South African producer,
Vitrex, was exported for the refurbishment of the historic 19
th
Century Hamilton Square Station, part of a large-scaled project to
improve all five Liverpool city centre Merseyrail loop line stations.
Vitrex cladding was already installed at
Liverpool Central (2012), Lime Street
(2013) and James Street (2013) stations,
and Vitrex has started supplying vitreous enamel
steel cladding also for Moorfields, the fifth, and
final, station to be upgraded and scheduled to
reopen in April 2016.
The aim of the R860-million overhaul of
the tube stations, owned by Merseyrail, is to
improve facilities for the increasing number of
passengers as well as modernise the stations with
better flooring, brighter lighting and improved
passenger information to plan their journeys
throughout the stations, says Cristian Cottino,
sales andmarketing director of Vitrex. Merseyrail's
chain of combined ticket offices and convenience
stores have also been upgraded.
Cottino says the Hamilton Square cladding
contract, secured by David Shepherd of Vitrex
Europe and Middle East, called for the provi-
sion of 1 000 m
2
of mainly 'Singapore White'
heavy gauge vitreous enamel steel panels, and
also 'Slate Grey' panels for the intersections of
adits and platforms. The contract included the
supply of curved panels, which had to be fitted
with acoustic linings, for the platforms of the
130-year-old station.
The panels were designed and specified
by the Berkshire, UK, company, SAS Project
Management, which also installed the cladding
panels and light boxes along the platforms, tube
tunnels and commuter walkways. In addition,
SAS Project Management (which collaborated
with Vitrex on the cladding installation at the
other Liverpool CBD stations), also installed 2 000
square metres of bespoke linear plank ceilings
TUBE STATION CLADDING
Historic Hamilton Square Station has become
the fourth Liverpool tube station to be clad
with vitreous enamel steel cladding supplied
by the South African company, Vitrex.
>
and upstands along the Hamilton Square station.
Vitreous enamel steel cladding panels have
been widely exported by Vitrex for several
decades now, particularly for installations at rail
stations in the UK, Ireland and the Far East. "An
important reason is that vitreous or 'porcelain
enamel steel' cladding, as it is sometimes called,
has specific properties that make it the ideal
solution in terms of durability, particularly in
high traffic areas such as underground stations,"
Cottino explains.
Among these benefits are:
•
Low maintenance: The wide variety of
colours available is permanent, non-fading
and the surface requires only simple,
periodic maintenance;
• Corrosion proof: The panels do not rust,
even in extreme marine conditions.
The coating is resistant to most alkalis,
acids, organic solvents and unaffected by
kerosene and vehicle emissions;
• Hygienic: The absence of pores on the
smooth, hard surface eliminates absorption
of dirt and grease, and reduces the presence
and growth of bacteria and mould;
• Resistance to abrasion: The hardwearing
surface is resistant to abrasive materials
with a surface hardness rating of between
6 and 7 on the MOH scale (Quartz has a
rating of 7).
• Vandal-proof and impact resistant: It is
extremely difficult to permanently mark the
surface with knives, keys and screwdrivers.
Unwanted graffiti and spray paint can easily
be removed;
• Non-combustible: Classified as 'Non-
combustible (A1)' in accordance with ISO
Standard EM 13501-1, the panels will resist
heat of up to 650 degrees Celsius and
continuous temperatures of up to 400 °C;
• Thermal shock: Resists extreme
temperature differentials and will withstand
rapid cooling by water spray from 400 °C to
room temperature over a 30-second period;
• Vermin-proof: The surface is impervious to
attack by rodents and boring insects;
• Acoustic and thermal insulation: Specific
performance requirements can be
addressed at the design stage.
• Environmentally friendly: The panels have a
working life of over 30 years with minimum
maintenance required. They also do not
need strong chemicals for cleaning, and are
fully recyclable
.
Malan says the in-situ concrete columns and
flat floor slabs without beams inside the office
ceiling voids, leave optimum space for services
reticulation. Galvanised steel members span
between the concrete fins to support window
shading panels and planter boxes.
“To minimise the cost and size of the
structural concrete elements, a lightweight
external walling system was employed.
It consists of pre-coloured steel sheeting to the
outside, insulation in the middle and drywall
boards on the inside: all fixed to lightweight
steel studs fixed between the floor slabs.
Window opening widths of over 5 metres
are achieved without heavy concrete or
steel lintels.
“Flashing details around windows and
joints are meticulously detailed. The drywall
system helped to speed up construction
by J.C. van der Linde & Venter Projects and
avoided the complications of wet trades at
heights,” Malan stated.
The bulk of office windows are orientated
north or south and are sheltered by expansive
aluminium filigree shading panels. Openings
on east or west facades are minimal and fully
protected by the aluminium filigree panels
over their full aperture.
Sustainability
“In the interests of further sustainability,
energy- efficient fluorescent and LED lights
are used with movement sensors to control
the lights to further reduce energy use. The
large, shaded glazed areas provide natural
light to supplement electric light. Dual flush
concealed cisterns and waterless urinals
reduce water use, and rainwater is collected
into roof tanks for irrigation of the planters on
the building.”
Malan concludes: “The use of fair face
concrete, face brick, galvanised steel and
pre-coloured sheeting makes for durable,
low-maintenance external finishes. External
plaster and paint is limited to a feature wall
at ground level. The building is designed to
• Client:
Duncharl Investments
• Main contractor:
J.C. van der Linde &
Venter Projects, represented by Stefan
van Wyk (contracts director), Ivan
Fick (site agent), and Elliot Tsotsetsi
(foreman)
• Architect:
Jeremie Malan Architects
• Consulting/structural engineer:
Otec
• Quantity surveyor:
Taljaard QS
• Electrical engineer:
C.A. du Toit
withstand the local climate and age gracefully
with the minimum of maintenance costs.
“The role of the contractors, J.C. van der
Linde & Venter Projects, in the completion of a
dream project must be mentioned. The build-
lers met the high quality requirements despite
limited time and site space and were part of
the professional team from the outset to final
completion,” he added.
CONSTRUCTION WORLD
APRIL
2016