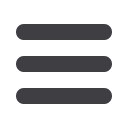

Industry
News
16
Wire & Cable ASIA – May/June 2007
Second hot-strip rolling mill for China
Metals Technologies (MT), a division of the Siemens Group
Industrial Solutions and Services (I&S), received another
order from Tangshan Guofeng Co Ltd, China, to equip its
second hot-strip rolling mill at the Tangshan location with
automation technology.
This includes all basic and process automation as well as
the visualisation system. A new strip-cooling model, which
is also part of the scope of supply, enables the efficient
production of high-quality steels.
Commissioning of the automation equipment of the new
rolling mill is scheduled for January 2008 and the first coil is
to be produced at the end of March 2008.
Tangshan Guofeng Co Ltd, located in Hebei province around
200km to the east of Beijing, operates a production com-
plex the capacity of which is to be doubled from a current
4.4 million metric tons of crude steel to 8.8 million metric
tons in the next few years. A new rolling mill will be installed
with a rolling capacity of up to three million metric tons of
hot strip per year and will be capable of rolling strip with
thicknesses up to 1,430mm.
Siemens is supplying the basic and process automation for
the reversing roughing stand equipped with a hydraulic
edger, a coil box, the seven-stand finishing train with work-
roll shifting and bending equipment, the laminar-cooling
section and the two coilers, including coil conveyor.
The technological control systems and the process models
for the individual mill sections are also included in the scope
of supply. Integrated HMI (human machine interface)
systems with easy-to-use process and plant diagnostic
functions will facilitate plant operation.
A central feature of the automation solution is the new strip-
cooling model of Siemens, which is based on a physical
description of the thermodynamic processes during cooling.
The calculation of temperature characteristic curves and
phase components along the entire strip is carried out in
real time. The current data is sent to a model-predictive
cooling-line control system.
As a result, precise monitoring of the entire strip cooling
procedure over time is possible. This not only ensures
constant quality for the whole strip, the required metallurgical
properties of the steel can also be reliably achieved within
tight tolerances. This enables the efficient production of
high-quality steel grades.
All of the components and systems to be used are part of
the integrated Siroll HM solution for hot-rolling mills. The
automation system is characterised by its high degree
of standardisation. This ensures rapid production start-up
and high plant availability.
Siemens is also responsible for the installation of the
supplied systems and supervision of the work as well as for
commissioning. The mechanical equipment and the drives –
mainly Siemens components – for the hot-rolling mill will be
provided by domestic Chinese companies.
Siemens – Austria
Fax
: +43 732 6980 3131
Website
:
www.siemens.com/metalsTenova receives order for
walking beam furnace
Italy’s Tenova Loi Italimpianti (formerly
Techint Technologies) designs and
supplies advanced technologies,
products and services for the metal
and mining industries. Thyssenkrupp
Steel AG, Germany, has awarded the
company a contract for the
engineering, fabrication, erection and
commissioning of one bilateral heated
walking beam furnace for its hot strip
mill in Bochum.
The furnace is designed for a capacity
of 250t/h to heat up slabs with different
qualities, and is equipped with
FlexyTech
®
Low-NOx high speed and
roof radiant burners. The new furnace
will be connected in series with three
existing furnaces, in order to increase
the mill load capacity and fulfil the
highest conditions in terms of
homogeneity of temperature, scale
losses, efficiency and emissions
control. The start-up of the complete
equipment will be in February 2008.
Tenova Loi Italimpianti – Italy
:
marina.landi@it.tenovagroup.comWebsite
:
www.tenovagroup.comCandor Sweden AB, provider of
surface treatment equipment for the
wire industry, has announced that it
will be represented in the USA,
Canada, Central and South America
by Bulk Chemicals Inc, USA.
Candor Sweden supplies both single-
and multi-strand systems for ferrous
and non-ferrous materials, and has
provided more than 300 plants for
different applications of surface
treatment of wire worldwide.
Applications
covered
by
the
company’s range include:
Plating – for electrolytic plating of
brass, copper, chromium, nickel,
silver, tin and zinc on ferrous and
non-ferrous wire;
Cleaning – single- and multi-strand
cleaning systems with bipolar
electrolytic degreasing and ultra-
sonic cleaning, or a combination
of both technologies;
•
•
Pickling – single- and multi-strand
pickling lines using hydrochloric
or sulphuric acid in line with hot
dip galvanising, phosphating and
electroplating;
Phosphating – single- and multi-
strand phosphating plants;
Candojet HW – patented high
speed hot water cleaning system
for high wire speeds;
Copperjet – high speed copper
coating unit for CO
2
welding wire
using the company’s own product
– the Inhibitor E1;
Bead wire – high speed bronze
coating for the automotive
industry.
Bulk Chemicals has a wide pro-
gramme of chemicals and lubricants
for the wire industry. Its range of
products incorporates new polymer
and traditional zinc phosphates, zinc
phosphate replacements, drawing
soaps and pre-coats for carbon and
stainless steel wire.
•
•
•
•
•
Candor Sweden AB expands USA business
Candor Sweden AB – Sweden
Fax
: +46 1112 6312
:
info@candorsweden.comWebsite
:
www.candorsweden.comBulk Chemicals Inc – USA
Fax
: +1 610 926 6125
:
info@bulkchemicals.usWebsite
:
www.bulkchemicals.us