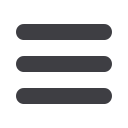

C
oating,
J
acketing & Galvanizing Technology
J
anuary
2008
www.read-tpt.com100
›
LOECO-INDUSTRIEANLAGEN
GmbH & Co. KG
Blötter Weg 141
D-45478 Mülheim a.d. Ruhr
Germany
Telefon +49 208 5 89 81 -0
Telefax +49 208 5 89 81 -24
loeco@t-online.de www.loeco.deThe most advanced manufacturing techniques and highest quality
materials are utilized to ensure uncompromising parts and performance.
Automatic Pipe
Galvanizing
■
Fume Control automated single-pipe-transport Pickling Line
■
Efficient Dipping/ Extracting/ Cleaning System for better
Coating Thickness Control
■
Acid Recovery and Flux Preparation
Experience of long-standing and the supply of more than 100 galvani-
zing plants to numerous countries around the world, guarantee the best
know-how and engineering. We design and supply hot dip galvanizing
plants of all kinds for structural parts and bulk goods and in particular
for pipes and tubes.
Galvanizing Equipment with
Engineering • Consulting • Turnkey Supply • Worldwide
11_200
6 4c Az 180x12518.10.200
6 16:57 Uhr Seite 1
SMS Demag AG, Germany, will supply
a host of comprehensive equipment and
machinery to the Magnitogorsk Metallurgical
Combine (MMK), Russia, due for startup in
2009 and 2010.
This equipment will be supplied to
secondary metallurgical facilities, and
includes a set of cold strip units with a
coupled pickling line and tandem cold mill,
and strip refining plant and equipment.
The supply scope comprises a ladle furnace
with two treatment stations, a duplex RH-
top facility, a deslagging stand and two ladle
treatment stations. The facilities will also be
used for producing pipe and shipbuilding
steels, which are to be processed in the 5m
heavy plate mill.
The cold rolling stage consists of a coupled
pickling line and tandem cold mill with an
annual capacity of approximately 2 million
tons. It is equipped with turbulence-tank
pickling technology and possesses five four-
high stands. The plant is claimed to be the
world’s most powerful coupled pickling line
and tandem cold mill, with high drive power
ratings and a rolling force of 35 MN per stand.
All stands operate with CVC plus
®
technology, with the final stand being fitted
with multi-zone cooling and the dry-strip
drying system. The facility is equipped with
the ‘Rotary Inspect’ inline inspection line, to
enable quality control during production.
The strip processing lines comprise the hot-
dip galvanising line and a combined hot-dip
galvanising line and continuous annealing
line, each with integrated skin-pass stands,
a recoiling and inspection line and two
packaging lines.
A noteworthy feature is the wide range of
materials, from mild to high-strength grades,
which are processed into galvanised
strip with GI and GA grades. Three acid
regeneration plants allow the pickling acid
to be fed back completely into the system.
SMS Demag AG
– Germany
Fax
: +49 211 881 4386
Website
:
www.sms-demag.comCoatings expert launches new Italian marine base
Socotherm Group has officially opened the new Modica-Pozzallo (Ragusa) marine
base in Sicily, Italy, a pipe coating plant for offshore market service. The new marine
base – aimed at the Mediterranean/North Africa regions – includes an outside area of
128,000m
2
and a covered area of approximately 12,000m
2
where internal and external
anticorrosion/thermal insulation (deepwater) coating plants have been erected. A
concrete weight coating plant and double joint fabrication rack will also be installed.
Socotherm offers pipe-coating services worldwide to the oil and gas industry, from
external/internal anticorrosion coatings to concrete weight coating and thermal
insulation. The group specialises in thermal insulation for the deepwater sector.
Socotherm Group
– Italy •
Fax
: +39 0426 901 055
:
info@socotherm.com•
Website
:
www.socothem.com
Advanced galvanizing, annealing and
pickling technology
n