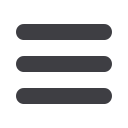

I
ndustry
N
ews
12
N
ovember
2009
www.read-tpt.com›
Higher balanced material output for larger wall PE pipes
Subsea training first from Hydratight
GROWTH and expansion in the cable
and energy markets has fuelled demand
for new extrusion technology for
manufacturing large wall piping of 4" to
20" in diameter (10.16 to 50.8cm) for a
host of industries including marine, cable,
electronics, oil, gas and water. Guill Tool &
Engineering Co’s technology for the 2030
Model is proving successful in serving
these markets.
Manufacturers of large wall pipes have
HYDRATIGHT has launched a new City and
Guilds-accredited range of subsea training
courses in mechanical joint integrity.
The courses, developed in direct
response to feedback from customers,
cover the use of hydraulic torque and
tensioning equipment for the subsea
sector and provide an insight into other
Hydratight subsea integrity equipment
such as flange pullers, nut splitters and
bespoke equipment.
Maintenance and fault finding issues
are also addressed, ensuring candidates
have a clear practical understanding of the
tools and equipment prior to mobilisation.
“Subsea joint integrity is a key issue
for the industry: mobilisation and time
frames are extremely critical. Downtime
for equipment due to lack of training and
safety considerations continue to add
significant but unnecessary time, and
consequently cost, to projects,” said Gary
Milne, Hydratight’s technical training
manager. “Subsea has traditionally
The Model 2030 tooling system
A diver trained by Hydratight on the City and
Guilds-accredited training course
The self-contained extrusion system
for the Model 2030 weighs from 6,000 to
10,000lb (2,721.55 to 4,535.92kg), and has
a patent-pending mounted track and cart that
enable easy handling and maintenance.
The cart system is engineered to tilt the
die on-the-fly, in order to compensate for
the catenary (sagging) effect caused by
gravity as the extrusion product exits the
equipment.
With the self-contained track support
system, one person can easily disassemble,
clean and re-assemble the system by sliding
the modular plates in and out of position
without using lifts or rigging equipment.
Pipe manufacturers that require large
diameters and multi-layer jacketing also
benefit from the advanced material flow
of the Model 2030 extrusion head and its
support system without rigging or support
equipment.
Guill Tool & Engineering Co
– USA
Fax: +1 401 823 5310
Email:
sales@guill.comWebsite:
www.guill.comIn Europe:
Padraic Lunn Enterprises Ltd
– Ireland
Fax: +353 71 9147604
Email:
plunn1@eircom.net“Legislation requires such skills and City
andGuilds accredited courses offer a platform
to provide these courses globally, with
industry best-practice provided by Hydratight
and its team of qualified experienced training
instructors. It’s a winning combination, for all
IMCA members,” said Mr Milne.
Hydratight
– UK
Fax: +44 12150 50800
Email:
training@hydratight.comWebsite:
www.hydratight.comlong experienced different polymer variations
in the end product that, in turn, forces a
slowdown in production and a critical loss
of time, material and money. Guill states
that with its new Model 2030, the extrusion
problem of accommodating an inconsistent
material flow and distribution has been
eliminated.
The Model 2030 tooling system
offers material distribution and product
consistency that is improved by a specially
designed, patent-pending combined die and
reservoir system.
With this precise tooling, material flow
from the die is delivered with the balance
necessary to achieve product accuracy. In
addition, a special co-extrusion capability
enables the simultaneous extrusion of
multi-materials or multi-stripes.
With Guill’s advanced flow analysis
software, the output of polymer is shaped
long before it reaches the tip of the die. With
this proprietary extrusion technology, the
polymer being distributed cannot return to
its original shape. The amount of required
material throughput for a pipe design is
channelled to meet the proper requirements.
After Guill’s design is complete, the
flow analysis software ensures that the
extrusion die is engineered to perform to
specifications.
suffered from a lack of attention when
it comes to accredited training. These
courses redress the balance.”
The courses are part of Hydratight’s
commitment to improve the skills needed
to reduce leakages on all assets within
industry sectors, while ensuring a clear
focus on the health and safety of all
personnel using high pressure hydraulic
torque and tensioning equipment.
To reduce risk it is essential for engineers,
divers and operators to become totally
familiar with all the equipment involved
in critical integrity issues. Such courses
delivered at the client’s premises or
Hydratight’s training academy offer clients
the opportunity to ensure the risk involved is
kept to a minimum.
Hydratight also works with The
Underwater Centre in Fort William to
deliver integrity courses as part of the
centre’s diver training programme for those
who want to use the equipment subsea
instead of through topside simulation.