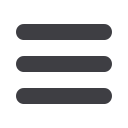

I
ndustry
N
ews
www.read-tpt.comN
ovember
2009
7
›
DIARY OF TUBE EVENTS
2009
NOVEMBER
2-3
Pipe & Tube Istanbul 09
Istanbul, Turkey
Technical Conference
:
info@itatube.orgWebsite
:
www.itatube.org13-16
Tolexpo 2009
Paris, France
Exhibition
:
mbazin@tolexpo.comWebsite
:
www.tolexpo.com15-18
Fabtech / AWS Welding Show
Chicago, USA
Exhibition
:
information@fmafabtech.comWebsite
:
www.fabtechexpo.com2010
FEBRUARY
10-12
Tube India 2010
Mumbai, India
Exhibition
:
dughl@md-india.comWebsite
:
www.tube-india.comMARCH
4-7
Boru 2010
Istanbul, Turkey
Exhibition
:
info@ihlasfuar.comWebsite
:
www.borufuari.comAPRIL
12-16
Tube / wire Düsseldorf 2010
Düsseldorf, Germany
Exhibition
:
infoservice@messe-duesseldorf.deWebsite
:
www.tube.de www.messe-duesseldorf.deMAY
24-27
Tube Russia 2010
Moscow, Russia
Exhibition
:
ryfischd
@messe-duesseldorf.de
Website
:
www.metallurgy-tube-russia.comSEPTEMBER
21-24
Tube / wire China 2010
Shanghai, China
Exhibition
:
tube@mdc.com.cnWebsite
:
www.mdc.com.cnOCTOBER
26-30
EuroBlech
Hannover, Germany
Exhibition
:
info@euroblech.comWebsite
:
www.euroblech.comNOVEMBER
2-4
Fabtech / AWS Welding Show
Atlanta, USA
Exhibition
:
information@fmafabtech.comWebsite
:
www.fabtechexpo.com2011
JANUARY
8-11
Tekno / Tube Arabia 2011
Dubai, UAE
Exhibition
:
alfajer@emirates.net.aeWebsite
:
www.tekno7.infoTube forming
performance for
safety parts
TUBE and Pipe bending and forming
machinery expert FELSS Burger GmbH,
Germany, recently delivered another
FU01-50 tube-forming machine to a
customer in the USA.
The turnkey solution has 16 NC
controlled stations feeding six metre
tubes Ø 22x2mm, cuts pieces to 200mm
length, chamfers, forms, stamps, punches,
checks, measures and sorts.
The system produces a highly safety
critical tube element for use in seat
belt restrainers.
With a patented process the wall of the
tube is first partly thickened. This allows
the tube to be widened and the resulting
part maintains a wall thickness of 2mm
throughout the product.
The tube widening is done in several
steps as the tube diameter is increased
and then formed to a characteristic
asymmetric nose.
Keeping the wall thickness constant
is key for this product due to the fact that
in case of a car accident an explosive
propellant will discharge a pressure of well
above 300 bar (4,500 PSI), which activates
the seat belt restrainer without destroying
the tube.
The installed machine’s robust and
controlled processes allow more uptime
and more output. This highly productive
unit achieves output capacity up to 20
parts per minute in a 7/7 mode.
All processes are precisely controlled
and run with little operator attention
allowing cost effective multi-machine
operations.
FELSS Burger has installed its online
machinery access, which allows software
to be updated, 24 hour/day trouble shooting
as well as visual check capabilities
via webcam.
In combination with FELSS Burger’s
tube bending units, such as FB61-21,
tubes can also be precisely bent three
dimensionally.
Additionally, in case of dynamically
changing pressures in a tube, Autofrettage
unit FA02-83 can be added and the
company says it significantly increases the
fatigue strength of a tube.
FELSS Burger GmbH
– Germany
Fax: +49 8361 920610
Website:
www.felss-burger.com