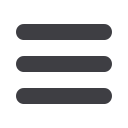

50
N
ovember
2009
www.read-tpt.com›
ORBIMATIC
Orbitalum Tools GmbH
Germany
Phone: +49 6408 9026 0
orbimatic@t-online.deORBIMATIC Ireland & UK Office
Phone: +44 1733 555 285
info@orbimatic.co.ukwww. o r b i ma t i c . c om
Next Generation
Orbital Welding
Equipment
ORBIMAT 165 C
A
dvanced
- Single dial operation
- Graphical operator guidance
- Auto programming
BUP Control
sectional control of inside purge pressure
Flow Force
reduces gas filling time of closed weld heads
down to 10 sec
Compatible with all
ORBIMATIC weld heads:
Enclosed
weld heads
Open arc
weld heads
Tube to tubesheet
weld heads
Visit us in
Hall I
Booth 229
T
echnology
U
pdate
A SUPER-THERMAL conductive mandrel
technology developed by Acrolab Ltd,
Canada, permits curing of filament wound
pipe and tube sections by heating the
mandrel uniformly, while rotating using
an Ambrell induction heating power
supply. Induction heating provides clean,
precise, even heat. This combination of
technologies eliminates the need for cure
ovens, saving time and energy.
Trademarked the ‘Isomandrel’, the new
mandrel design consists of a process
internal to the mandrel that enhances its
thermal conductivity and thermal reactivity.
The process permits heat to be applied in a
localised concentration that is then rapidly
and homogeneously redistributed over the
complete mandrel working surface.
Isomandrel technology, when coupled
with induction heating, permits the mandrel
and filament winding to continue rotating
while being heated to an optimum controlled
temperature to effect cure. This heating
occurs while the assembly is still rotating in
the winding machine or on a rotating fixture
within the manufacturing cell.
Acrolab Ltd, working with McClean
Anderson Inc, USA, and Ameritherm, an
Ambrell company of ScottsvilleNewYork, as
a technology team, constructed the curing
PHAMITECH Int’l, China, has launched
a new solid state HF welder that uses
high-power MOSFET IXFN38N100Q2
38A/1000V and fast recovery diode DSEI
2x61-12B 60A/1200V from IXYS Germany
to form inverting circuit in series (VFI).
The modularised design enables a more
compact structure, easier maintenance
and high-power realisation.
The equipment is safety guaranteed
by bridge-divided over-current protection
technology.
Advanced control technology, such as
fixed angle phase-locking control and upper/
lower limit frequency lock-lost protection,
makes the equipment more stable and
efficient, with more accurate and effective
protection to the inductor open circuit and
short circuit problems during pipe welding.
The solid state HF welder is designed
with advanced electronic load matching
cell at McClean Anderson’s laboratory. The
induction heated Isomandrel curing station
was used to cure a number of 48" long
pipe sections wound with glass and carbon
fiber epoxy pre-pregs, provided by TCR
Composites of Ogden Utah. They were
wound on a 3" OD Isomandrel.
At the end of the winding cycle, the
sections were successfully cured on the
Isomandrel using an Ambrell induction
heating power supply and coil assembly
while the Isomandrel and winding were still
mounted and rotating at a reduced 10 RPM
on the Super Hornet Winder.
By providing high thermal energy
uniformly over the entire mandrel surface
outward through the filament winding, the
cure is completed in a shorter time, with less
energy, while providing a significantly more
uniform cure and resin rich ID. Ameritherm
and McClean Anderson are currently
developing a fully software/hardware
integrated station to provide the controlled
power and recipe requirements to integrate
with Acrolab’s Isomandrel technology.
Ambrell
– USA
Fax: +31 65486 59044
Email:
info@ambrell.comWebsite:
www.ambrell.comtechnology (PS+PWM control), which can
ensure the welder works at the highest
efficiency, maximum power factor (>0.9)
and optimal load matching status, and to
allow simple switchover between induction
welding and contact welding mode.
An optional speed-power closed-loop
control system can improve welding
efficiency and reduce the technical
adjustment period.
A step-up/step-down rectifier trans-
former for the HF welder power supply
is not required, which has energy-saving
benefits compared with electron tube
welders or parallel type solid state
welders.
Phamitech Int’l Company Ltd
– China
Fax: +86 10684 70948
Email:
sales@phamitech.comWebsite:
www.phamitech.comCure of thermoset filament wound
pipe sections with induction heat
Solid state high frequency
welder technology from China